The sustainable development of the conventional construction industry has been hampered by intensive labor consumption as well as huge construction and demolition waste (CDW). A study in the journal Construction and Building Materials considers the implications of 3D printing mortar using recycled aggregates.
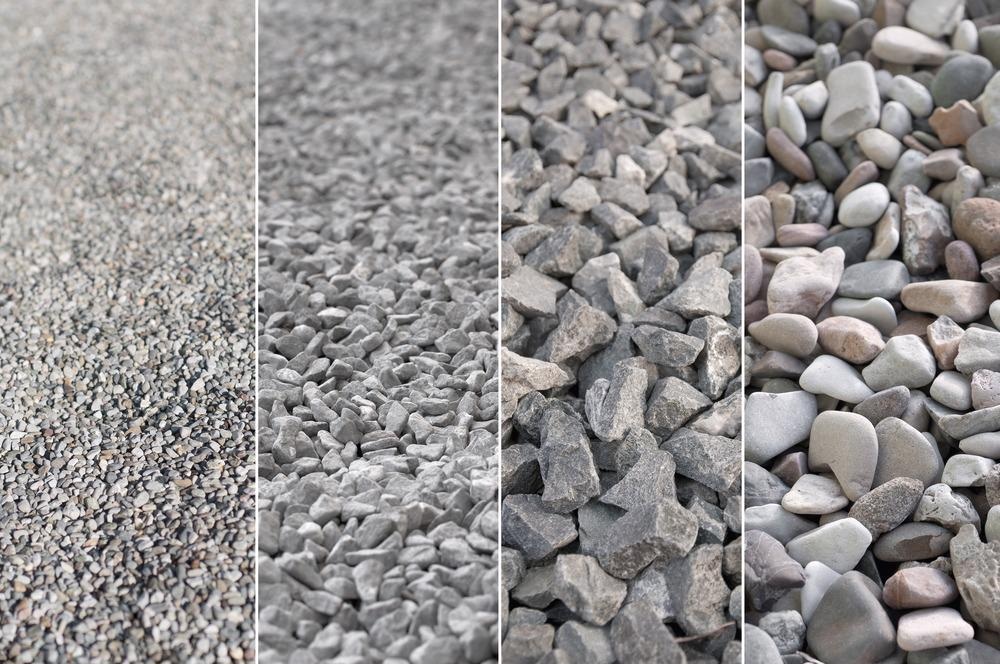
Study: On rheology of mortar with recycled fine aggregate for 3D printing. Image Credit: mahey/Shutterstock.com
The process of 3D concrete printing (3DCP) is a kind of digital manufacturing method that can linearly deposit cementitious mixtures layer upon layer to form structures without formworks, thereby reducing labor requirements.
Recycled concrete made using recycled materials from CDW offers not only similar mechanical properties but also higher economic and environmental benefits than conventional concrete. However, studies on the use of recycled materials from CDW in 3DCP are still limited. Thus, the addition of recycled fine aggregates (RFA) into 3DCP is significant and will produce benefits in the sustainable development of the construction industry.
This study investigates the viability of using recycled fine aggregates (RFA) in 3D mortar printing (3DMP) by assessing the properties of 3D printing (3DP) mixtures with different contents of RFA (0%, 50%, and 100%) and sodium gluconate (0%, 0.6%, and 1.2%) both before and after high-rate shearing.
Experiment
P.O 42.5 Ordinary Portland cement and river sand were respectively used in this study as cementitious material and fine aggregate. The RFA selected was derived from waste concrete with the original cube compressive strength in the range of 20–25 MPa.
The waste concrete was first obtained from the demolished concrete, and then it was shifted to a C&D waste recycling plant for crushing into recycled coarse aggregates and recycled fine aggregates. Polycarboxylate-based superplasticizer, hydroxypropyl methylcellulose (HPMC), and sodium gluconate were used as admixtures to tune the printability of the 3DP mixtures.
The printing system included four subsystems: mechanical subsystem, controlling subsystem, feeding subsystem, and extruding subsystem. The effective operating space of the mechanical subsystem was 3.0 m, 3.0 m, and 4.0 m in the directions of X, Y, and Z, respectively. The 30-mm-diameter printing nozzle was controlled by the CNC system with the highest moving speed of 120 mm/second.
At present, there is no recognized testing standard for the buildability of 3DCP. To achieve a more accurate expression of buildability, the mixtures were printed layer-upon-layer as high as possible in the form of a circle with 300 mm diameter. The width and height of each printed segment were 30 mm and 15 mm, respectively.
The maximum printing height, average vertical strain for all layers, the average vertical strain caused by both compression and stretching were measured to describe the buildability of 3DP mixtures.
Results
The time-varying curves between shear stress and time for the five 3DP mixtures were plotted at the resting time of 0 min before and after high-rate shearing. The shear stress of all curves increased initially to a peak value and then decreased to an equilibrium value.
This is because the flocculation structure produced by the cement hydration can resist the shearing process to some extent. However, after that, the flocculation structure is broken and the cement mortar changes from a solid-like state to a liquid-like state. Here, the peak value is defined as the static yield stress, which refers to the shear stress needed to start the material flow.
The replacement of river sand with RFA increased the static yield stress of the 3DP mixture, but the addition of sodium gluconate decreased the static yield stress. High-rate disturbing has an evident impact on the rheology of these 3DP mixtures, which caused a shapely decrease in the static yield stress.
The results showed that the incorporation of RFA highly increased the 3DP mixture’s initial value and time-varying rate of the static yield stress, viscosity, and area of thixotropy hoop. By contrast, the addition of sodium gluconate decreased them, respectively.
Conclusion
The incorporation of RFA highly increased the 3DP mixture’s initial value and time-varying rate on the static yield stress, viscosity, and area of the thixotropy hoop. However, later, it improved its buildability and impaired its extrudability and open time.
The addition of sodium gluconate into the 3DP mixture with 100% RFA can positively improve its extrudability and open time because of its retarding effect on decreasing the initial value and time-varying rate of static yield stress, viscosity, and area of thixotropy hoop.
Meanwhile, the printing mixture with 100% RFA + 1.2% sodium gluconate maintains good buildability. High-rate shearing has a significant effect on the rheological properties of 3DP mixtures with/without RFA. Thus, a feeding system that can provide high-rate and continuous shearing is recommended in practical printing.
Journal Reference:
Zou, S., et al. (2021) On rheology of mortar with recycled fine aggregate for 3D printing. Construction and Building Materials. https://www.sciencedirect.com/science/article/abs/pii/S0950061821030531