Nature creates structures that supersede advanced conventional materials in terms of complexity and mechanical properties. Taking inspiration from bamboo, a team has now demonstrated a 3D printing method for toughening polylactic acid, as published in the journal Polymer Testing.
Microscope photo of a cross-section of a bamboo stem. Study: PLA toughening via bamboo-inspired 3D printed structural design. Image Credit: ChWeiss/Shutterstock.com
Why Nature is a Superior Architect of Functional Materials and Complex Structures
Nature creates vastly more complex structures than conventional artificial ones. Whilst much progress has been made in advanced materials research, the fact remains that nature is the superior architect. Evolution has given organic systems a distinct edge over the attempts of scientists to copy them.
Structures such as wood, carapaces, antlers, beaks, bones, and bamboo have superior mechanical properties because of their complex internal structures. Cellular components, as well as solid support systems, have evolved over eons to suit their dedicated purpose perfectly. Hexagonal and polyhedral cells have specific and unique structures which confer elevated levels of stiffness and strength.
External stimuli such as mechanical load also affect the arrangement of the structural building blocks during adaptive growth and when undergoing remodeling during an organism’s lifespan. Both deposition and removal of material are employed during remodeling, whereas in adaptive growth organic material is deposited in a specific way.
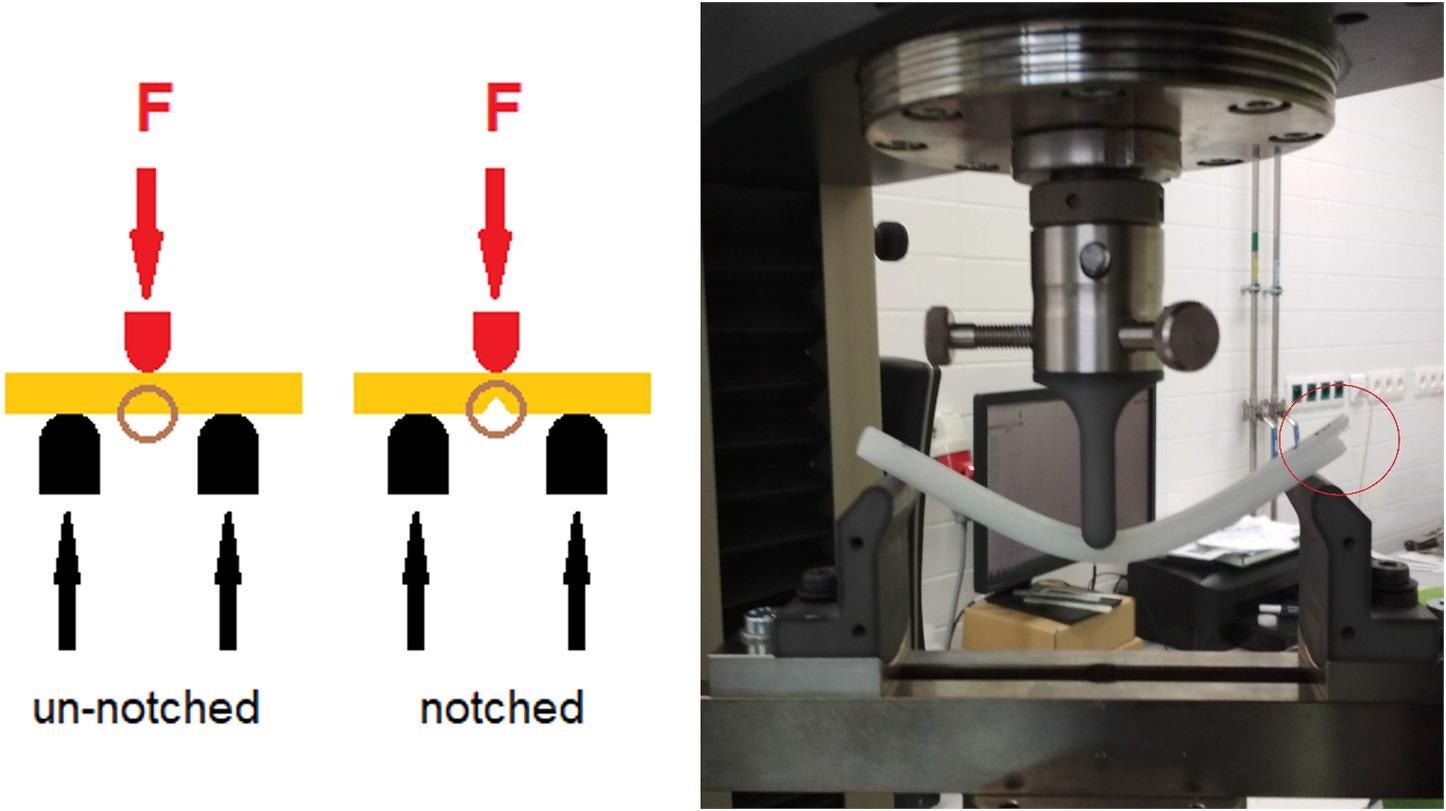
A scheme of experimental testing (left) and an image of real-time three-point bending test of the un-notched 3D printed specimen (right) – delamination can be seen in the red circle. Image Credit: Svatik, J et al, Polymer Testing
Bamboo has become the focus of research into creating superior artificial foams. The functional foams found in bamboo plants exhibit a porosity gradient which provides a gradation in properties. The cell walls are formed by biopolymers which are reinforced by nanoparticles. Localized mechanical properties are dependent on nanoscale structural arrangement. Overall mechanical performance of the natural material seems to be governed by spatial distribution, and cell shape, and size.
Therefore, bamboo is an attractive target for investigating how natural structures can inform the design of artificial foams with superior mechanical and physical properties. One material that can benefit from this process is polylactic acid (PLA), an interesting material that shows much potential for 3D printing advanced materials research.
Polylactic Acid: An Overview
Polylactic acid is a biodegradable polymer that has received attention in recent years due to its unique properties and superior ability to be processed into 3D printable ink. However, it has one major drawback: it becomes brittle after a few hours at room temperature. Advanced applications require a material to be reliable and structurally sound, so this disadvantageous property must be addressed by materials scientists.
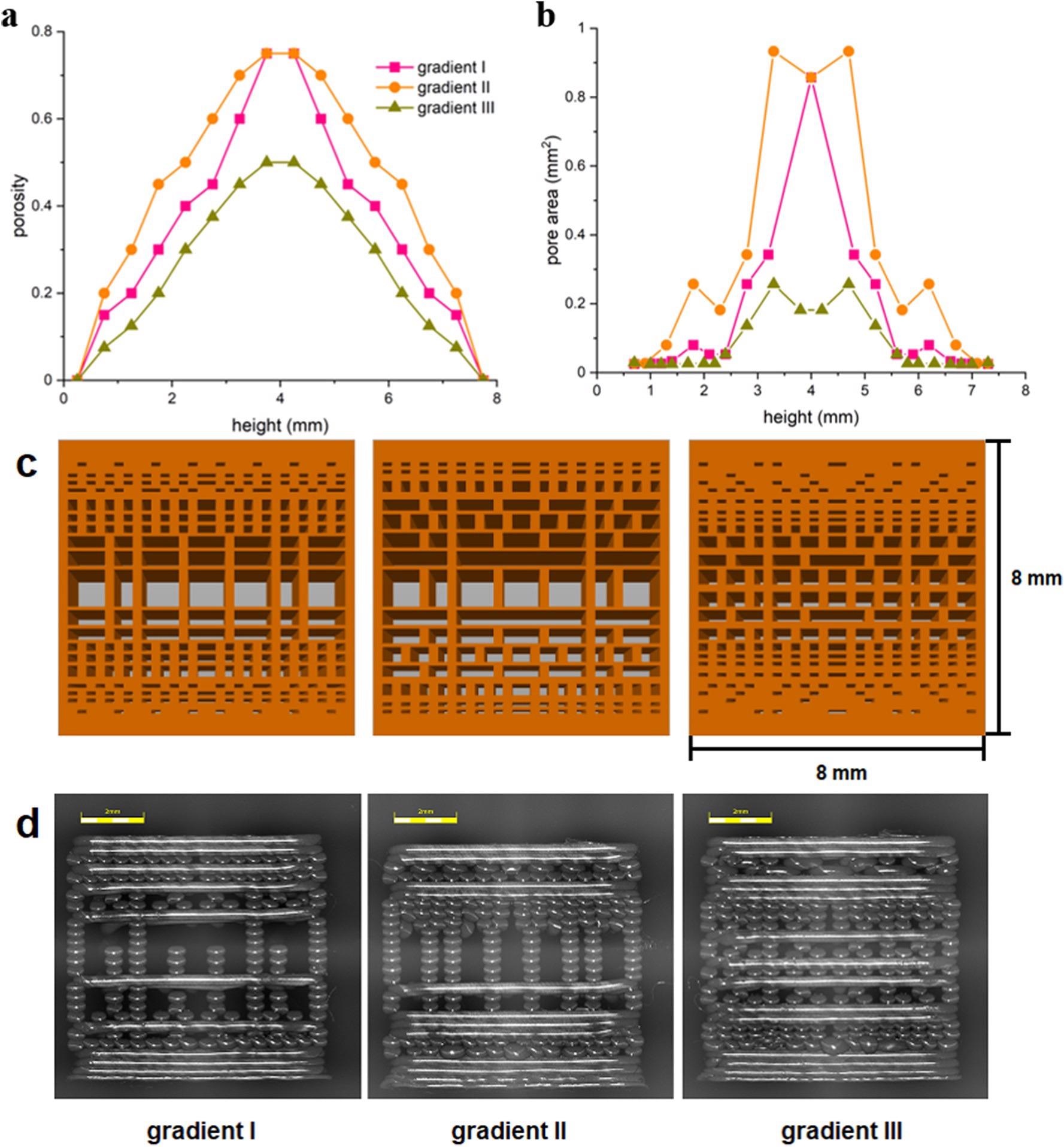
Porosity trend (a.) and average area of a single pore (b.) in gradient specimens with respect to their placement across the specimen height (the lines are just guides for the eye); c. Design detail of the gradient specimens investigated in the x-z plane; d. CLSM images of gradient 3D printed samples (scale bar is 2 mm). Image Credit: Svatik, J et al, Polymer Testing
Recently, composition modification has been the subject of several studies to reduce this brittleness and improve the material’s properties. This presents further issues, as using this approach makes other properties worse and makes the manufacturing process less sustainable. A better solution is therefore needed to fabricate this commercially important 3D printable polymer.
Improving the Properties of PLA With a Nature-Inspired Process
Taking inspiration from bamboo, research from a team led by Juraj Svatík has demonstrated a new method to improve the mechanical and physical properties of polylactic acid. This process is known as fused deposition modeling.
Porous structures of polylactic acid similar to the internal structure of bamboo were 3D printed using this process. Polylactic acid was toughened purely by the resulting pore gradient. This controls energy dissipation throughout the entire three-dimensional structure. Properties such as ductility were improved, especially in notched samples.
By strengthening the physical and mechanical properties of polylactic acid, the possibility of its wider use for advanced applications is increased, and the work lays the foundation for future toughened 3D printed structure design. Gradient porous materials will be able to be used in structural components for many innovative 3D printed products.
Other Current Bio-Inspired Methods in Advanced Structural Materials Research
Bio-mimicking is gaining traction in advanced materials research. Alongside the technique described in the research paper, many different processes inspired by natural hierarchical structures are being explored. There has been research into artificial woods, which whilst emphasizing the formation of oriented channels and strong walls, has proven difficult to create walls of strength similar to natural wooden structures.
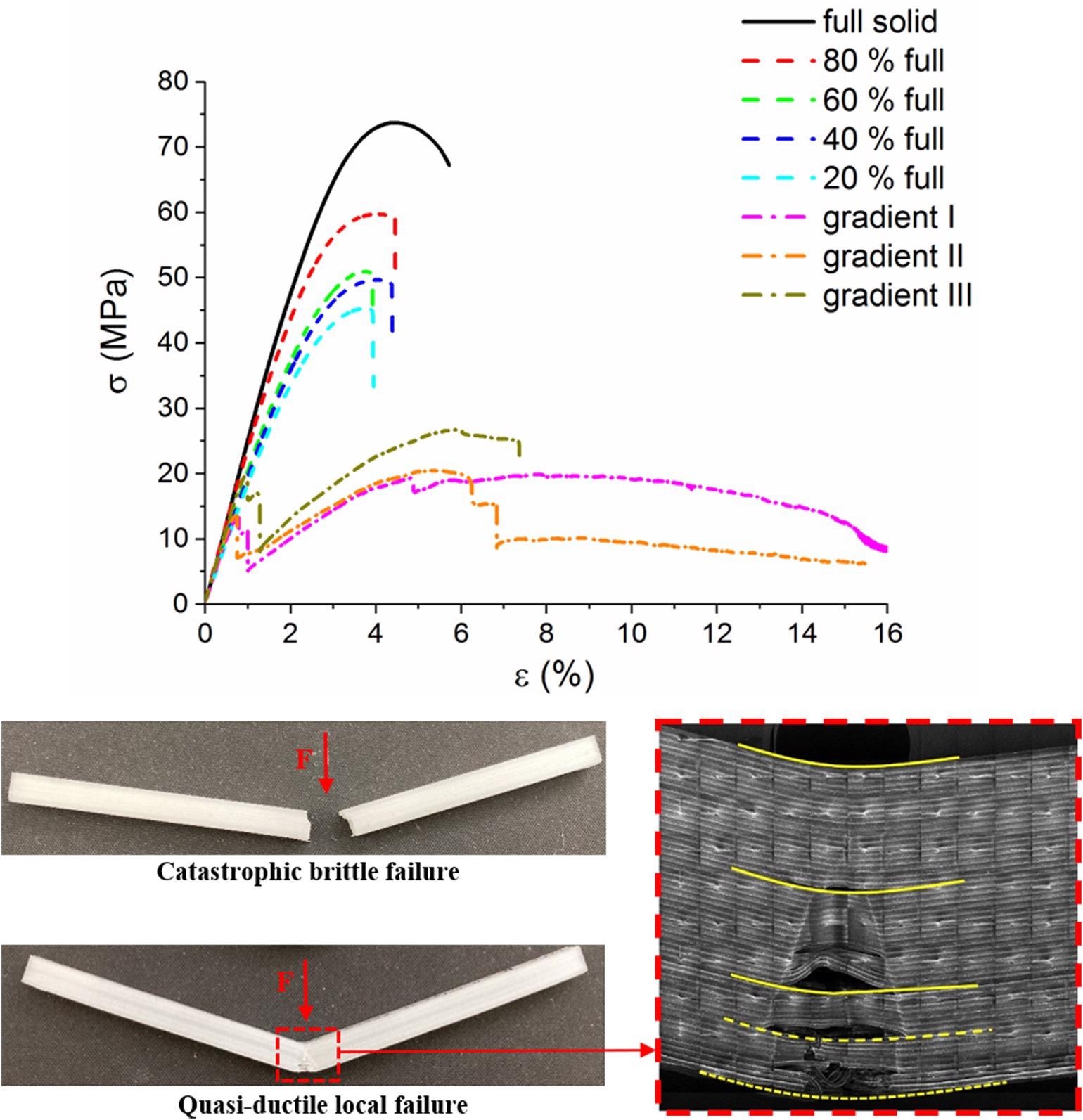
Stress-strain curves of PLA samples with various porosity and 3D printed design deformed in three-point bending (top). Comparison of failure modes of specimens after 3-point bending test with an SEM image detail of quasi-ductile local failure (bottom) – red arrows indicate the direction of the acting force (F), full yellow lines indicate intact layers, dashed lines indicate gradually failing layers. Image Credit: Svatik, J et al, Polymer Testing
Sandwich structures are examples of incredibly strong bio-inspired materials. The load is carried by two thin plates, and an internal honeycomb structure transfers shear stress, inspired by both human skulls (the plates) and bees (the honeycomb structure.) This structure has been shown to have superior stress absorption capabilities and has a low density. This makes these structures ideal for applications where stress dampening is required, such as battery housing in electric vehicles.
The Future
Inspiration from nature is helping to inform the direction of key areas of advanced materials research. The research from the team of Svatik et al to develop bamboo-inspired 3D printable polylactic acid with superior mechanical and physical properties will help to design sustainable structural materials for multiple advanced applications.
Further Reading
Svatik, J et al. (2021) PLA toughening via bamboo-inspired 3D printed structural design [online] Polymer Testing 104 10740 | sciencedirect.com. Available at: https://www.sciencedirect.com/science/article/pii/S0142941821003494
Disclaimer: The views expressed here are those of the author expressed in their private capacity and do not necessarily represent the views of AZoM.com Limited T/A AZoNetwork the owner and operator of this website. This disclaimer forms part of the Terms and conditions of use of this website.