Utilizing additive manufacturing processes for the printing of functional integrated thermoelectric devices has huge potential for the field of materials science. Research published in ACS Energy Letters has explored this subject, presenting a state-of-the-art summary and outlook of the development of additive manufactured thermoelectric materials and devices.
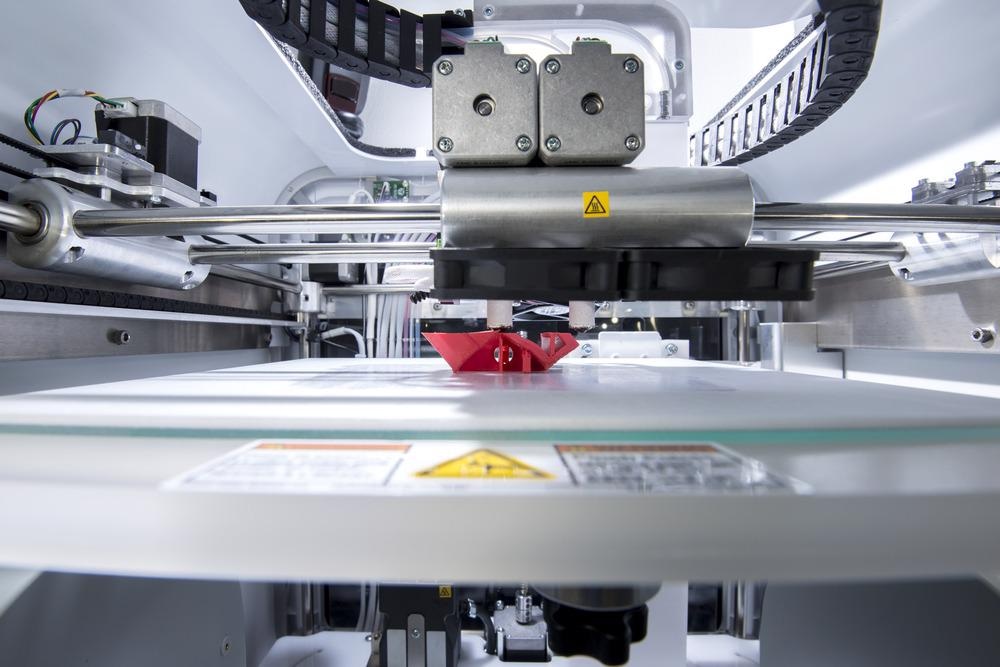
Study: Additive Manufacturing of Thermoelectrics: Emerging Trends and Outlook. Image Credit: RomboStudio/Shutterstock.com
Thermoelectrics
The field of thermoelectrics is a mature one. Since the discovery of thermoelectric materials two hundred years ago, research has progressed significantly. Recent studies have reported superior thermoelectric performance and techniques for fabricating both traditional and novel materials have become well-established.
Recent advances in the field currently have particular relevance due to the development of low-power technologies such as Internet of Things (IoT) and wearable devices. Moreover, the urgent need to rapidly decarbonize industry and reach net-zero emissions has facilitated interest in alternative energy sources for new generations of devices.
There has been increasing interest in utilizing thermoelectric materials for battery-less sensors, self-powering tech, and on-chip cooling. Thermoelectrics can play a dual role as thermoelectric generators and thermoelectric coolers. The performance of these materials on a systems-level depends on factors such as device quality and the performance of materials. On a materials level, performance is governed by properties such as working temperature, electrical and thermal conductivity, and the Seebeck coefficient.
Due to the challenges in constructing thermoelectric devices, device design and manufacturing methods have not been studied as much as materials properties in recent years. Fabrication methods such as zone melting and hot pressing are used for thermoelectric materials, which are complex and energy-consuming. Materials tend to be bulky and rigid. Devices are limited in terms of geometrical complexity and practical application. Moreover, in contrast to other semiconductor technologies, research into scaling thermoelectric devices is less mature.
Implementing thermoelectric components into wearable devices to utilize latent body heat is a popular research direction currently. Work has been undertaken to introduce flexibility into thermoelectric devices, with some studies using materials such as liquid-metal embedded elastomers. Other studies have explored thermoelectric material deposition onto flexible substrates.
3D Printing Thermoelectric Devices
Additive manufacturing, otherwise known as 3D printing, is one of the pillars of Industry 5.0. This technological field has advantages in overcoming the challenges of thermoelectric device design and scalability. For instance, promising progress in using 3D printing to fabricate thermoelectric generators with versatile shapes has been made in recent years.
There are many different additive manufacturing methods that are commercially available. These include vat photopolymerization, powder bed fusion methods, materials jetting techniques, and extrusion-based methods such as direct ink writing. Each has its own particular pros and cons, and some methods are not suited for 3D printing of thermoelectric materials.
Amongst the various 3D printing technologies currently developed, direct ink writing (DIW) has shown particular promise for fabricating functional thermoelectric devices with complex architectures and enhanced flexibility. This method deposits ink (also termed “slurry”) layer-by-layer through an extrusion nozzle.
Extrusion printing methods such as DIW have several advantages. The large range of inks and materials that can be used for extrusion printing facilitates the possibility for fabricating fully printed multi-material thermoelectric devices. Direct ink writing also has benefits in terms of cost-effectiveness, less materials waste, and lower energy consumption.
Given the recent emergence of 3D printed thermoelectric materials (within the past decade) the zT value of these materials is not as competitive as their conventionally fabricated counterparts. The zT value quantifies the material’s thermoelectric performance. However, due to the advantages of additive manufacturing over conventional fabrication methods and the potential for further optimization, direct ink writing is a promising process for the manufacture of high-performance thermoelectric devices.
The Study
The focus review published in ACS Energy Letters provides an insight into the field. Formulation and device strategies for the fabrication of high-performance thermoelectric materials and devices have been explored. The authors have noted that there is a lack of literature from the perspective of improving device and material function by leveraging the printing formulations and capabilities of 3D additive manufacturing.
The study starts with a summary of various 3D printing technologies and evaluates them as suitable techniques for thermoelectric material and device fabrication. Research elaborating on direct ink writing and its use for this purpose are explored, with a specific focus on DIW methodologies for fabricating inorganic thermoelectric inks due to their higher zT values than organic inks.
Lastly, the focus review investigates the performance gaps between 3D-printed thermoelectric materials and their conventionally fabricated counterparts to address issues and provide a perspective on future research directions for the field which will overcome these performance gaps.
Further Reading
Zhang, D et al. (2022) Additive Manufacturing of Thermoelectrics: Emerging Trends and Outlook [online] ACS Energy Lett. 2022 (7) pp. 720-735 | pubs.acs.org. Available at: https://pubs.acs.org/doi/10.1021/acsenergylett.1c02553
Disclaimer: The views expressed here are those of the author expressed in their private capacity and do not necessarily represent the views of AZoM.com Limited T/A AZoNetwork the owner and operator of this website. This disclaimer forms part of the Terms and conditions of use of this website.