A new paper published in Polymers has reported the vat polymerization of intricate, lightweight sandwich structured materials using photovoltaic liquid resin. The research has been conducted by scientists from the Southern Illinois University Carbondale.
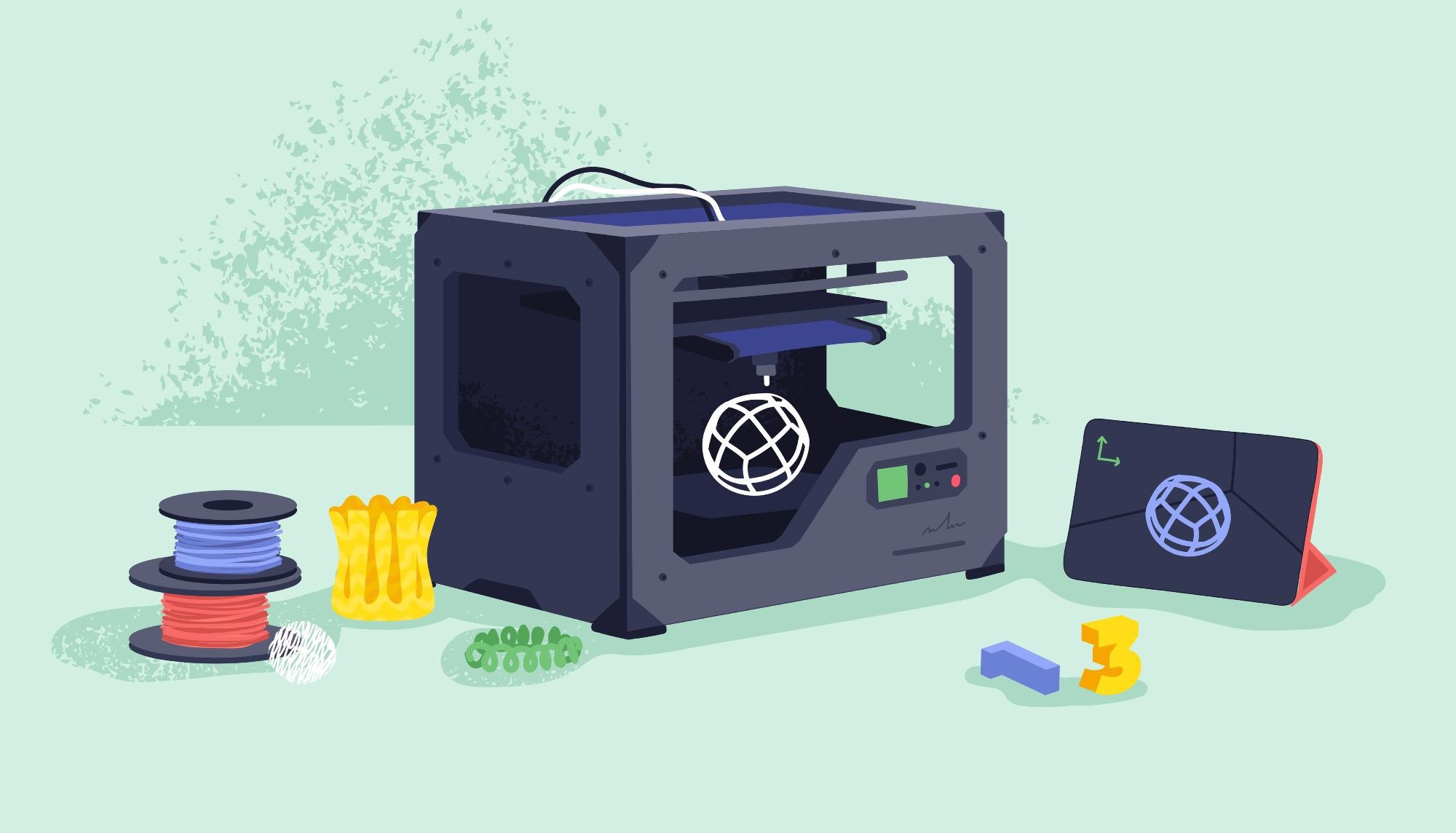
Study: Performance Evaluation of Sandwich Structures Printed by Vat Photopolymerization. Image Credit: art_inside/Shutterstock.com
Sandwich Panels
Sandwich panels consist of three layers – two thin skins (face sheets), and a thick core layer. These panels have found application in construction, the aerospace industry, the military, automotive parts, as energy-absorbing materials, acoustic attenuation, thermal insulation, and so forth. The layers can be constructed of either the same or different materials depending on the application.
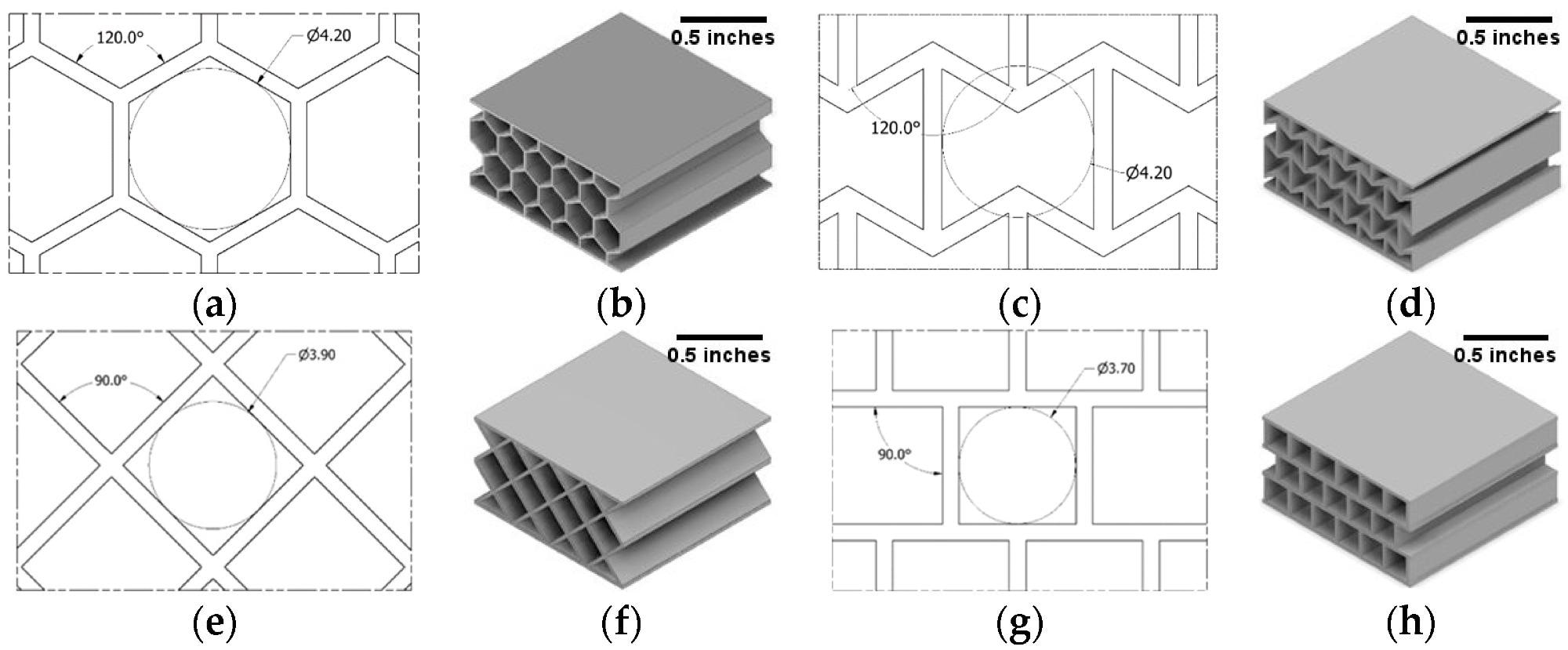
Design of unit cells of (a) honeycomb, (c) re-entrant honeycomb, (e) diamond, and (g) square. The wall thickness of all cellular walls and face walls is set to 0.5 mm. (b,d,f,h) are the complete CAD drawings of sandwich panels with different cellular structures. Image Credit: Nath, S.D & Nilufar, Polymers
The properties of a sandwich panel depend on the materials used in the core and facesheet layers, as well as the core structure's topology. The core layer of a sandwich panel consists of a low-density cellular structure. Amongst the shapes studied for the cellular core of sandwich panels, honeycomb structures are the most common. Honeycomb shapes possess superior out-of-plane energy absorption and are strong and lightweight.
Other structures studied include diamond and rectangular shapes, which are simple and possess attractive physical properties. Flexural tests have indicated that diamond-structured cores are superior to honeycomb structured cores and possess good in-plane and out-of-plane performance.
Auxetic structures, which have a negative Poisson’s ratio, have also been investigated in recent years. Although auxetic structures may not be as lightweight, strong, or stiff as other structures, they possess advantageous properties such as high energy absorption, shear resistance, and good ballistic resistance, making them attractive for several engineering applications.
Manufacturing Sandwich Panels
Conventional manufacturing processes involve multiple fabrication steps, can only produce limited core topographies, and do not have the required design flexibility. Recently, additive manufacturing (3D printing) has demonstrated its potential as a manufacturing process to overcome the issues with conventional methods.
Additive manufacturing techniques offer easy, tailored fabrication of complex cellular morphologies for use in sandwich panels. However, optimizing these techniques is crucial to printing cellular core structures with adequate properties, as identical structures manufactured with both conventional and additive manufacturing methods can differ and different 3D printing technologies can produce structures with different properties.
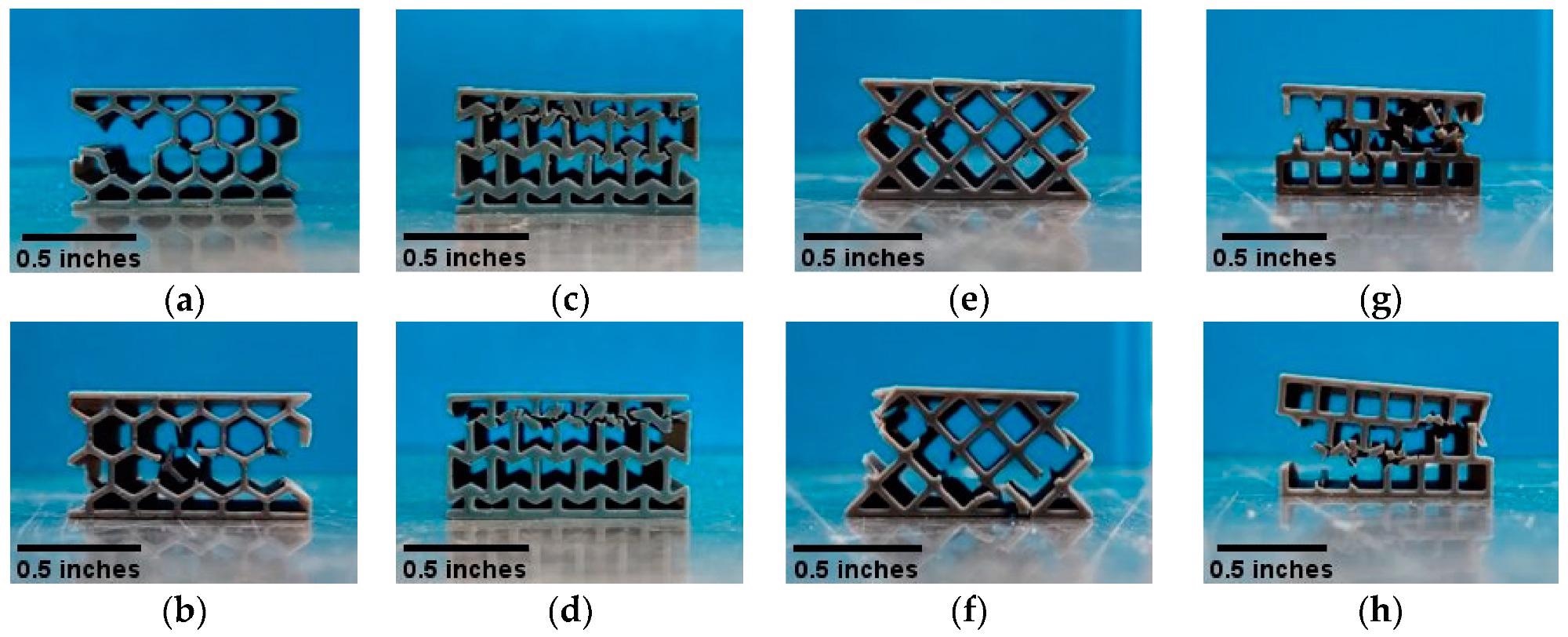
Representative images showing the failure after the compression test. (a,b) honeycomb; (c,d) re-entrant honeycomb; (e,f) diamond; (g,h) square sandwich panels. Image Credit: Nath, S.D & Nilufar, Polymers
Several studies have been performed in recent years to investigate the potential of additive manufacturing processes to fabricate complex core architectures in sandwich panels. The properties of printed structures have been evaluated by several researchers. Flexural tests have indicated that different printed structures have different failure modes. One study has demonstrated that diamond structures possess the highest flexural and compressive strength, whilst corrugated structures have the highest tensile strength, for instance.
Whilst the properties of structures produced using different techniques have been evaluated thoroughly in current research, the mechanical behavior of sandwich panels with different printed cellular structures printed using vat polymerization is still poorly understood.
The Study
To investigate the potential of vat polymerization methods for producing sandwich panel cores, the team behind the research has printed core layers with square, conventional honeycomb, re-entrant honeycomb, and diamond structures. The authors have characterized the thermochemical properties of the printed sandwich panels.
Uniaxial compression tests were used in the research to elucidate each panel type’s specific strength and compressive performance, and finite element analysis was employed by the authors to provide a better understanding of stress distribution under compressive loading. The authors conducted dynamic mechanical analyses to investigate how the properties of the sandwich panels changed under varying temperatures.
Results of the Study
Results of the tests demonstrated that the printed diamond structure possessed the highest strength and compressive modulus. Under compressive loading, the square, honeycomb, and diamond structures all demonstrated catastrophic failure, although the core walls in the diamond structure bent under compressive loading, distributing the stress. The facesheets of sandwich panels with diamond core structures also fractured under compressive loading.
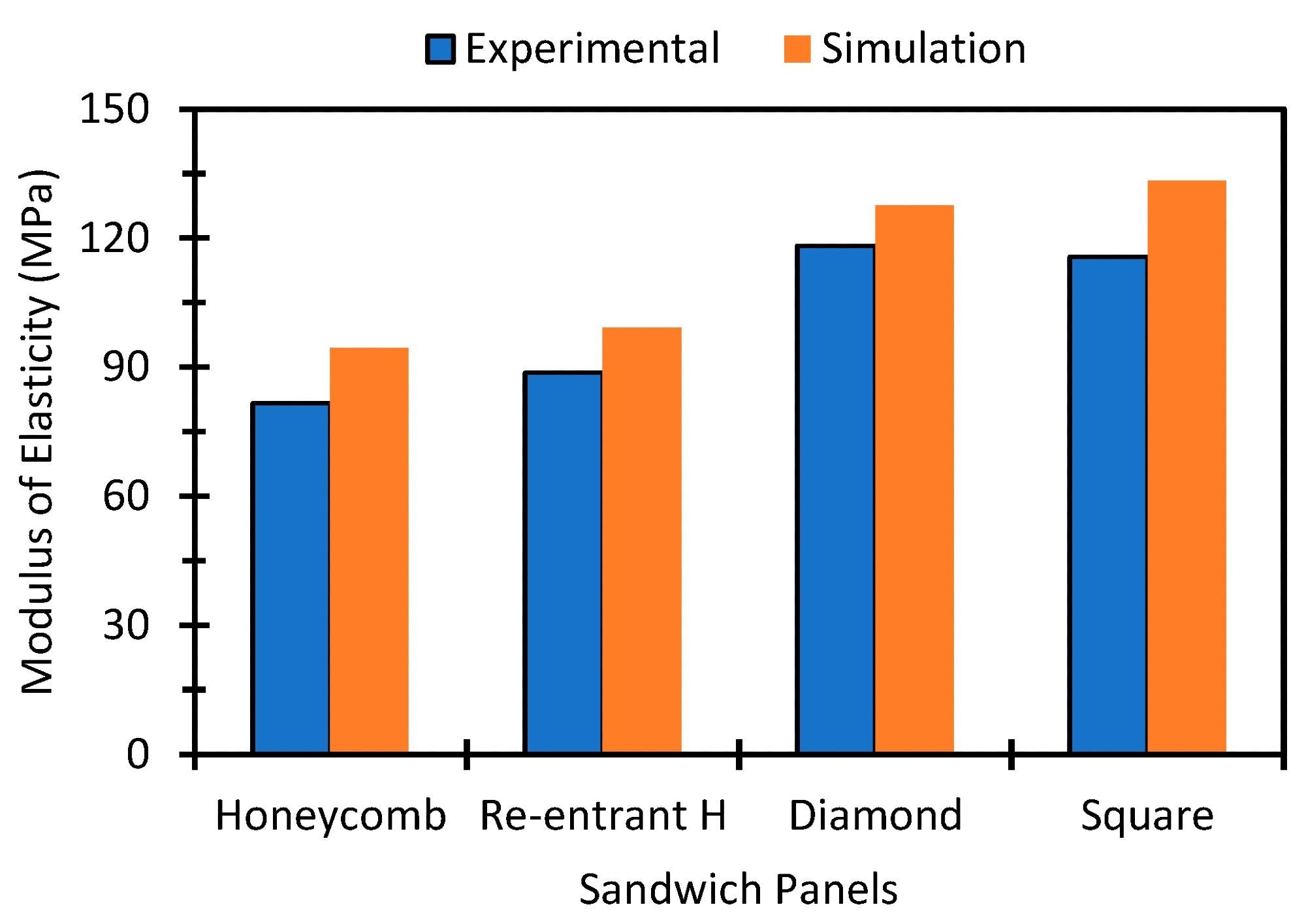
Comparison of the compressive modulus of the experimental and simulation results of different sandwich panels. Image Credit: Nath, S.D & Nilufar, Polymers
Re-entrant honeycomb samples possess a homogenous stress distribution, leading to a failure throughout each core layer in the sample. This caused predictable fracture behavior and a higher strain resistance and increased the structure’s capacity to absorb energy.
In terms of deformation patterns, stress concentration, and stress-strain data, the experimental and numerical analyses were observed to be in good agreement. The results of the dynamic mechanical analysis of the sample materials demonstrated that they were stable at higher temperatures but, compared to solid structures, possessed a lower storage modulus.
Changing factors such as wall thickness and core topology can tailor the sandwich panel’s properties, and the properties can vary by changing the printing technique. Overall, the authors have stated, the study provides important insight into the properties and performance of sandwich panels that incorporate vat polymerization-printed cellular core materials.
Further Reading
Nath, S.D & Nilufar, S (2022) Performance Evaluation of Sandwich Structures Printed by Vat Photopolymerization [online] Polymers 14(8) 1513 | mdpi.com. Available at: https://www.mdpi.com/2073-4360/14/8/1513
Disclaimer: The views expressed here are those of the author expressed in their private capacity and do not necessarily represent the views of AZoM.com Limited T/A AZoNetwork the owner and operator of this website. This disclaimer forms part of the Terms and conditions of use of this website.