By Surbhi JainReviewed by Susha Cheriyedath, M.Sc.May 3 2022
In an article recently published in the journal Additive Manufacturing, researchers discussed the machine learning prediction of melt pool characteristics (MeltpoolNet) in metal additive manufacturing.
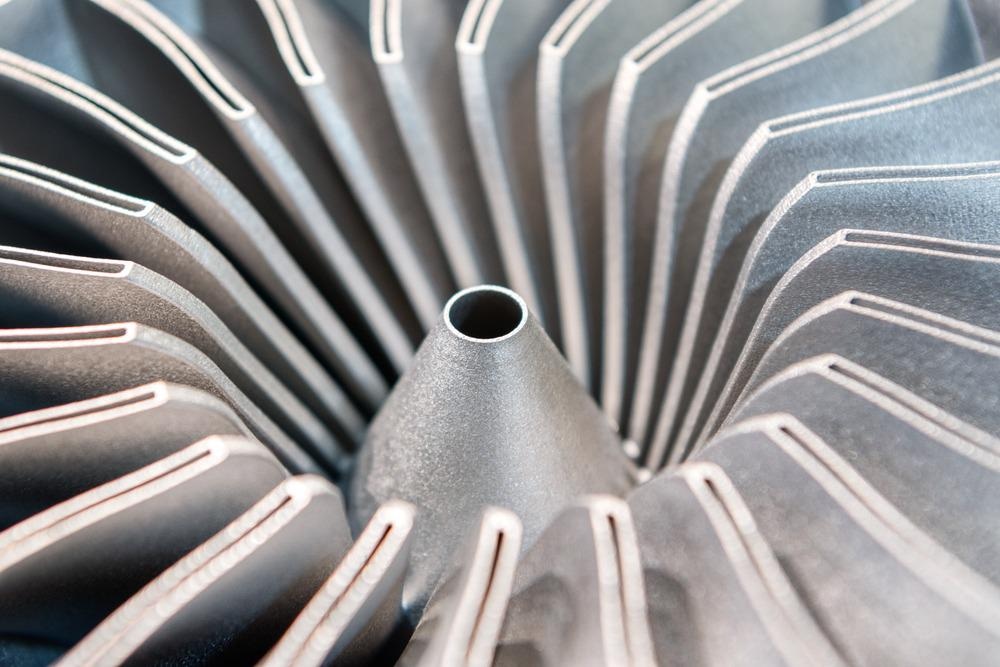
Study: MeltpoolNet: Melt pool characteristic prediction in Metal Additive Manufacturing using machine learning. Image Credit: Nordroden/Shutterstock.com
Background
Metal additive manufacturing (MAM), a novel and innovative manufacturing technology that enables sophisticated component fabrication, has prepared the path for the next industrial revolution. MAM can manufacture parts and components with complicated shapes using specialty metals and materials.
Increasing the scale, speed, and quality of printed products are still huge problems, despite the fact that additive manufacturing has drawn a lot of scientific and technical work in industry and academia. Various experimental monitoring approaches are frequently used to find the optimal processing window for part manufacturing with low faults.
Due to the multi-physics and multi-scale character of AM processes, along with the major impact of the processing parameters on the printed products, AM has shifted from purely physics-derived approaches to data-driven and physics-based approaches. As a result, machine learning (ML) and data-driven analysis have become standard procedures in advanced manufacturing applications, and AM research is becoming increasingly popular. Creating ML models for metal additive manufacturing, on the other hand, necessitates solving obstacles associated with data scarcity.
About the Study
In this study, the authors discussed a complete methodology for the benchmarking of ML for melt pool characterization. More than 80 MAM publications were used to compile a large experimental dataset that included MAM processing settings, meltpool size, materials, meltpool modes, and defect types. To establish a comprehensive learning framework for meltpool defect and shape prediction, physics-aware MAM featurization, evaluation metrics, and adaptable ML models were used.
The benchmark used by the authors was based on a wider set of data, which allowed for the improvement and regulation of component quality across a greater range of materials and processing parameters. The proposed dataset contained a minimum of 80 sources of experimental data gathered from studies performed on a small number of alloys using a single AM method. These diverse data sources were combined into a broader repository for melt pool characterization across a diverse range of alloys and processing parameters. A set of AM machine learning methods dubbed MeltpoolNet was built to characterize melt pool behavior.
The researchers used MeltpoolNet to build ML models using the complete experimental dataset. MeltpoolNet allowed for the optimization of melt pool processing parameters and the prediction of porosity in printed products. Experiments with various materials, processing parameters, and MAM process types were included in the dataset.
The impact of various build process settings on the performance of the proposed models was also illustrated. In addition, a data-driven and model identification method was created to uncover clear relationships between dataset processing parameters and material qualities, which was more interpretable than ML models.
Observations
The accuracy of the classification job was 85.6% when the XGBoost model was used to forecast melt pool classification by using the parameters of the baseline, absorption coefficients, and elemental featurization. With a model configuration of the baseline features and material one-hot encoding as the input to the random forest algorithm, the best result was attained with 85.78% accuracy. The gradient boosting model achieved a 99.55% accuracy and a mean absolute error (MAE) of 10.92 µm.
Gradient boosting, neural networks, and random forest defeated other ML models for regression and classification. It was also shown that feature engineering in AM was critical for the production of a generalizable and highly accurate ML model.
The proposed explicit models were not only more interpretable than the used ML models, but they also had better meltpool geometry prediction ability than the Rosenthal meltpool geometry estimate.
Conclusions
In conclusion, this study presented a complete machine learning benchmark for predicting melt pool geometry and fault kind. Data from a wide range of AM melt pool characterization experiments were gathered. To improve the accuracy of different ML models, various approaches to feature engineering for AM input data were introduced. Multiple machine learning models were compared to one another using different featurization strategies. In addition, evaluation measures and reporting standards were also explored.
Furthermore, data-driven explicit models for estimating meltpool geometry from process parameters and material properties were found, which exceeded Rosenthal's estimation for meltpool geometry while retaining interpretability. In addition, based on the dataset processing parameters and material attributes, a data-driven model identification method was created to estimate the meltpool geometry.
The authors believe that this benchmark can be used to control melt pools and optimize processes. They expect that by offering a consistent platform for comparison and evaluation, this benchmark will make it easier to optimize and regulate additive manufacturing processes and that MeltpoolNet will become a comprehensive resource for the metal additive manufacturing machine learning community.
More from AZoM: How is Fast Fourier Transform Used Alongside Electron Microscopy?
Disclaimer: The views expressed here are those of the author expressed in their private capacity and do not necessarily represent the views of AZoM.com Limited T/A AZoNetwork the owner and operator of this website. This disclaimer forms part of the Terms and conditions of use of this website.
Source:
Akbari, P., Ogoke, P., Kao, N-Y., et al. MeltpoolNet: Melt pool characteristic prediction in Metal Additive Manufacturing using machine learning. Additive Manufacturing 102817 (2022). https://www.sciencedirect.com/science/article/pii/S2214860422002172