By Surbhi JainReviewed by Susha Cheriyedath, M.Sc.Jul 5 2022
In an article recently published in the journal Additive Manufacturing, researchers discussed how to create a fully integrated melt electro-writing 3D printer from conception to completion.
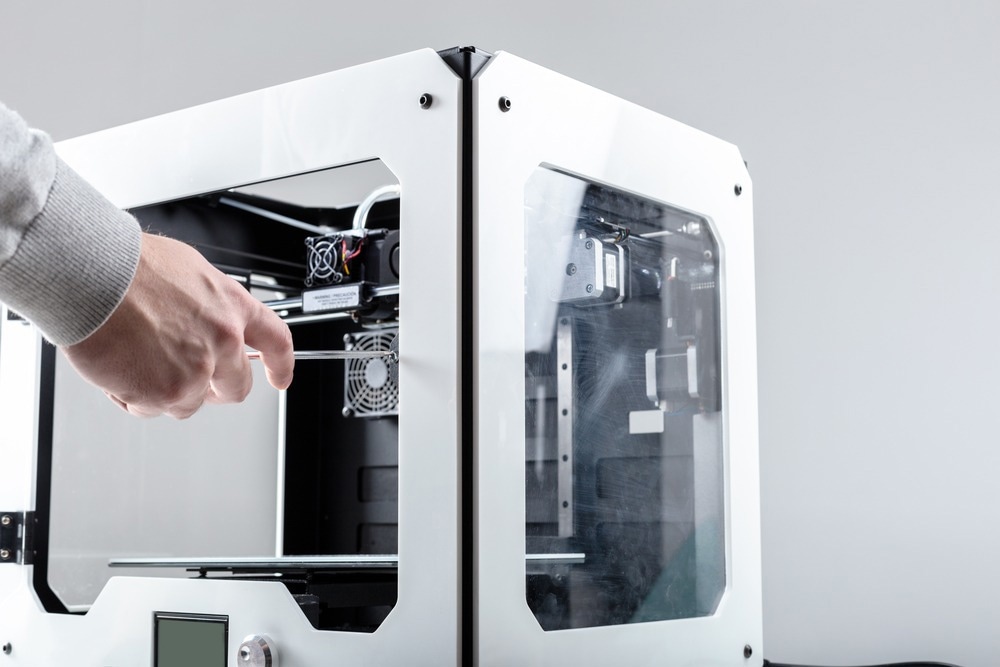
Study: How to design, develop and build a fully-integrated melt electrowriting 3D printer. Image Credit: FabrikaSimf/Shutterstock.com
Background
Using a high voltage between a print nozzle and collector to stabilize the flow of print material and enable accurate and controlled deposition of micron to sub-micron diameter fibers, melt electrowriting (MEW) is a high-resolution additive manufacturing technology. MEW has seen remarkable growth and development since its beginnings, despite the fact that this technology is still in its relative infancy.
Even though a number of businesses have developed and started offering MEW printers on the market, many researchers still employ custom-made systems. There are several options for creating a customized MEW printing system, ranging from less expensive, more straightforward, and reasonably easy-to-implement systems to sophisticated, fully automated systems with real-time process monitoring.
The construction of more complicated structures with changing fiber sizes will be possible with further integration of other elements, such as a pressure source. The heaters' integration largely benefits usability because it may be turned off automatically at the end of a print run.
About the Study
In this study, the authors discussed the creation, conception, and construction of a unique MEW printer with complete integration between all essential parts. The motion system, print head, and safety systems were described in detail. The several ways that could be utilized for each system in a bespoke MEW printer were illustrated, which provided the reader with a description of how it might be developed based on the particular needs of the end customer. The printer's capacity to create tissue engineering scaffolds with various material topologies was demonstrated.
The team explained how these systems were connected via a central control unit to provide pre-programmed dynamic control over printing variables, which enabled the fabrication of a variety of advanced material designs with applications in regenerative medicine, tissue engineering, and other areas.
The researchers documented the whole design and construction of a unique MEW printing system with two nearly similar printers. The complete integration of all essential components, which provided the user with complete control over processing parameters and allowed for the fabrication of a variety of biomaterial scaffold designs, was one of the advanced features of these MEW printers that were not present in the majority of commercially available systems.
In-depth information on the development of the framing, print head assembly, motion system, a rotating mandrel for tubular scaffolds, as well as complete wiring and integration details for all of these parts to a central control unit was provided.
Some of the primary abilities of these printers, such as the capability to print large volume scaffolds with layer-by-layer voltage control, nanoscale fibers printing, and hybrid printing capabilities was demonstrated by combining both MEW additive manufacturing principles and fused deposition modeling (FDM), the fabrication of variable fiber diameter scaffolds via automated fiber stabilization and layer by layer extrusion pressure control, and printing of complex geometries via drawing exchange format (DXF) files, and subsequent printing of the tubular MEW scaffolds.
Observations
It was shown that 20 μm diameter MEW fibers could be placed on 200 μm diameter FDM flames to create hybrid scaffolds using FDM printing. With 30 μm fibers deposited in one direction and 10 μm in another at a 90° offset, it was also demonstrated that variable fiber sizes could be defined by pressure variations. When working with extremely stable polymers like PCL, it was discovered that having the barrel heater temperature about 5 °C lower than the nozzle yielded more consistent fiber than using equal or higher temperatures. The threshold over which arcing could potentially happen was greatly increased by the much higher dielectric strength of 24 kV/mm of Ketron PEEK compared to air.
A variety of applications in tissue engineering and beyond could be made with the help of MEW, a potent additive manufacturing technology that had a lot of potential for the production of complicated, micrometric resolution scaffolds.
Conclusions
In conclusion, this study described how to design and construct a unique MEW printer with cutting-edge automation and fabrication capabilities. The authors demonstrated the importance of the different systems utilized in a MEW printer and highlighted a number of additional alternatives and strategies that may be used depending on the particular needs of the end-user.
By first educating those who are interested in creating similar custom devices and, in addition, giving potential and current practitioners in this developing area of additive manufacturing research an understanding of the inner workings of MEW technology, this work seeks to increase the accessibility of MEW technology.
More from AZoM: What is Glow Discharge Optical Emission Spectrometry
Disclaimer: The views expressed here are those of the author expressed in their private capacity and do not necessarily represent the views of AZoM.com Limited T/A AZoNetwork the owner and operator of this website. This disclaimer forms part of the Terms and conditions of use of this website.
Source:
Eichholz, K. F., Gonçalves, I., Barceló, X., et al. How to design, develop and build a fully-integrated melt electrowriting 3D printer. Additive Manufacturing 102998 (2022). https://www.sciencedirect.com/science/article/pii/S2214860422003918