In an article recently published in the journal Additive Manufacturing, researchers discussed the impact of process temperature on vat-photopolymerization in hot ceramic lithography of silica-based ceramic cores.
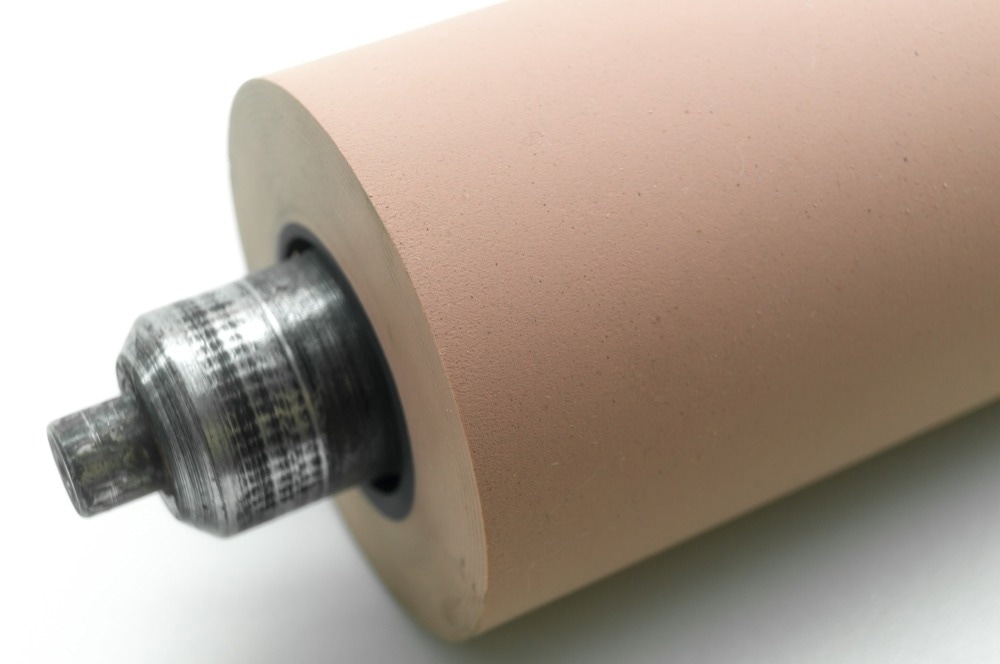
Study: Hot ceramic lithography of silica-based ceramic cores: The effect of process temperature on vat-photopolymierisation. Image Credit: Ireshetnikov54/Shutterstock.com
Background
Due to their lightweight, sustainability, robustness, and other high-performance characteristics, ceramics are finding increasing use in the aerospace industry as well as many other industries. In the quest for more fuel-efficient turbines, the complexity of the cooling channels and, consequently, their ceramic cores, is greatly desired.
Due to the ceramic cores' ever-increasing geometric complexity, ceramic additive manufacturing (AM) has emerged as the most practical production technique for the development of complicated parts in the future. The traditional method of producing ceramic cores, known as ceramic injection molding (CIM), needs high-pressure injection equipment and complicated, expensive, and time-consuming injection dies.
Vat-photopolymerisation (VPP) is the most widely used commercial ceramic printing technology. Stereolithography (SLA) is the oldest VPP technique. The other two VPP methods, which were created more recently, are liquid crystal displays (LCD) and digital light processing (DLP). According to earlier research, the mechanical properties of the green bodies can be improved by lowering the overall viscosity of ceramic inks and raising the reactivity of the photocurable (meth)acrylate monomers (binder combinations).
However, one of the process elements, the print temperature, can also be quite important. Only a small number of research have been conducted to look into how heat affects the polymerization, mechanical characteristics, and conversion rate of photopolymers, despite the fact that several commercial printer manufacturers provide preheated vat systems as a ready solution.
About the Study
In this study, the authors described an enhanced-temperature vat photopolymerization of ceramic-loaded mixes, also known as hot ceramic lithography, which was utilized to 3D print silica-based ceramic cores for hot section components of aero and industrial turbines. The degree of polymerization of the base resin binders and the rheological behavior of the ceramic slurry, as well as hot lithography, could both have a substantial impact on the pre-and post-sintering qualities of the 3D printed ceramic objects.
By doing tensile, dynamic mechanical analysis (DMA), and Fourier-transform infrared spectroscopy (FTIR) analyses on binder-only prints, the authors sought to better understand how various printing temperatures would alter the properties of the basic binder combinations prior to loading ceramic particles.
The team assessed how higher printing temperatures affected the mechanical characteristics of binder combinations loaded with ceramic. When the process temperature was set closer to the binder combinations' initial glass transition temperature, the base binder and the ceramic-loaded mixtures both produced the highest mechanical characteristics. When compared to traditional room-temperature vat photopolymerization printing, the proposed printing temperature was higher to improve the mobility of monomers and active species but lower than the amount that caused heat-induced cross-linking.
The researchers examined the impact of temperature on the rheological behavior and peeling forces of highly loaded ceramic-laden mixtures (61.2 vol. % of SiO2-ZrSiO4). At a process temperature of 35 °C, the suspension demonstrated a strong transition from shear-thickening to shear-thinning behavior, which was excellent for perfect ceramic 3D printing. At 25 °C, the suspension exhibited shear thickening behavior, which made it difficult to replenish the slurry during printing. The mixture's viscosity increased at very low shear rates, which had an impact on peeling forces, as print temperature increased to 45 °C and subsequently 55 °C.
Observations
According to the findings, the printing temperature had a considerable impact on the mechanical properties of components and the conversion rate of base binders. A positive association existed between process temperature, ultimate tensile strength (UTS), and conversion rates when the impact of print temperature on the mechanical characteristics of the base binder was examined.
When the printing temperature surpassed the Tg of the binder system, a negative impact on the mechanical properties of the parts was noticed. A closer match between the ceramic suspension print temperature and the initial Tg of the binder material could also greatly increase the green strength of ceramic objects. Due to the greater volume fraction of the SiO2-ZrSiO4 addition, the highly ceramic-loaded binder mixes used in this work showed shear thickening behavior at 25 °C.
This shear thickening behavior prevented the slurry from being replenished consistently during the printing of big, complicated pieces, which led to layer delamination and, ultimately, deformations in the prints after the sintering. The heat had an impact on the critical shear of both ceramic suspensions, which showed a rapid transition from shear-thickening to shear-thickening behavior at high temperatures.
When the process temperature was increased from 35 to 55 °C, the viscosity of the mixture at next-to none shear significantly increased. The most significant finding of the rheology investigation was the absence of obvious peaks in viscosity at 35 °C during printing or between print cycles, which suggested a near-Newtonian behavior at this optimal temperature for both suspensions. The complex-shaped cores having B-37 suspension failed during the printing and sintering processes when printed at temperatures over 35 °C.
The results of the peeling tests showed that the degree of cross-linking and reactivity of the binder mixes was more harmful to the peeling forces than the increased viscosity at elevated temperatures of 45 °C and 55 °C. This was corroborated by the fact that B-37 exhibited lower viscosity than B-42 at elevated temperatures, but the peeling force data showed a reversal trend, with the B-42 mixture recording lower peeling forces than B-37 as a result of lower reactivity and crosslinking density at these temperatures.
Conclusions
In conclusion, this study elucidated an enhanced-temperature VPP of ceramic-loaded mixes, or so-called hot ceramic lithography in order to print silica-based ceramic cores using commercial LCD-screen stereolithography. The ceramic suspension was printed at 35 °C temperature and made with the B-37 binder mixture and were the best mixture and print parameter choices. The validation study demonstrated how hot ceramic lithography could be used to successfully print complex-shaped ceramics with great dimensional precision.
Because of their increased efforts to reduce their carbon footprint, producers of turbine and jet engines were able to create components that were both more complicated and fuel-efficient. The increased cross-linking density and the base binder's reactivity resulted in a stronger adhesion between the cured layers and the printer's clear film, which resulted in higher separation/peeling pressures.
The authors mentioned that hot ceramic lithography at the proper printing temperature could address a variety of print and post-print concerns, resulting in ceramic components that are stronger and more dimensionally accurate.
They also stated that this study offers a method for determining the ideal printing temperature for ceramic printing VPP applications based on base-binder and ceramic-loaded mixes.
More from AZoM: What are Sand Batteries and Can They Solve the Sustainable Energy Crisis?
Disclaimer: The views expressed here are those of the author expressed in their private capacity and do not necessarily represent the views of AZoM.com Limited T/A AZoNetwork the owner and operator of this website. This disclaimer forms part of the Terms and conditions of use of this website.
Source:
Ozkan, B., Sameni, F., Goulas, A., et al. Hot ceramic lithography of silica-based ceramic cores: The effect of process temperature on vat-photopolymierisation. Additive Manufacturing 103033 (2022). https://www.sciencedirect.com/science/article/pii/S2214860422004250