In a paper recently released in the open-access journal Energies, researchers used national institute of standards and technology (NIST) real gas simulation models and the modified k-ɛ turbulence for the numerical simulation of rapid filling of high-pressure hydrogen storage cylinders. They also optimized the hydrogen cylinder’s internal structure without a precooling condition to reduce the maximum cylinder temperature and enhance the state of charge (SOC).
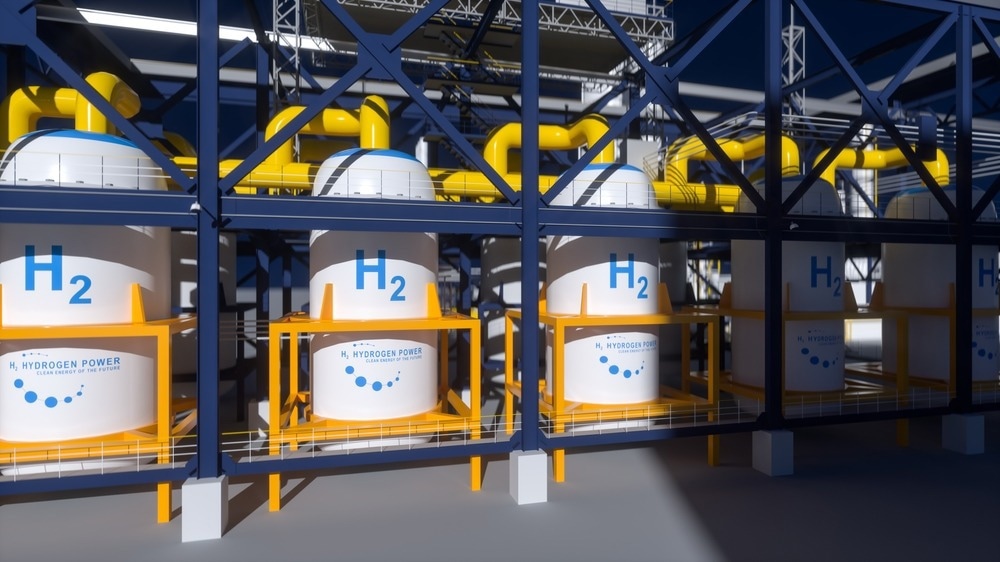
Study: Numerical Simulation and Optimization of Rapid Filling of High-Pressure Hydrogen Storage Cylinder. Image Credit: Audio und werbung/Shutterstock.com
Background
A key requirement for the industrialization and application of hydrogen energy is a safe, economic, and highly efficient hydrogen storage technology. As of today, hydrogen is compressed and stored in cylinders that have broad temperature adaptability, low energy consumption, and high technical maturity.
However, the fast hydrogen charging of the cylinder causes a temperature rise effect and, along with the high pressure, it can impact the mechanical characteristics of the resin matrix as well as reduce the SOC and the cylinder’s fatigue life. There is a risk of damage to the cylinder when the temperature exceeds 85 °C or goes below -40 °C. When the SOC is under 90%, the cylinder is inefficient and underfilled, while an overfilled cylinder poses a safety hazard.
Recent studies on the influence of pressure and temperature rise during hydrogen injection established a computational fluid dynamics (CFD) model. The studies largely focused on type III and type IV injection parameters, fiber materials, and cylinder lining and their effect on the cylinder’s temperature. However, studies considering the cylinder’s internal structures and the low SOC caused due to the temperature rise have been limited.
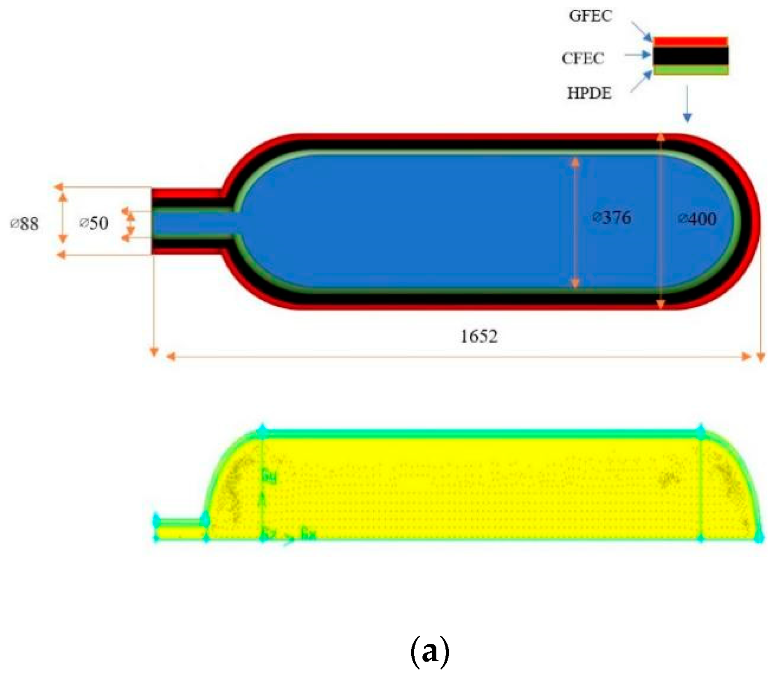
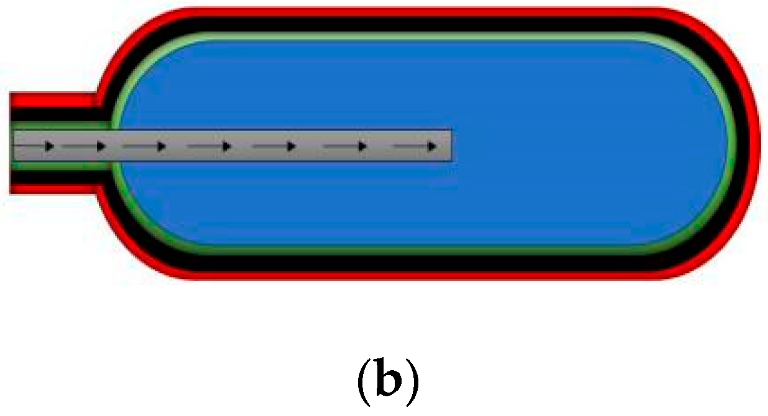
Two-dimensional geometry and computational grid of the cylinder before and after optimization (dimensions are given in millimeters): (a) Original scheme, (b) Optimized scheme. Image Credit: Xue, L et al., Energies
About the Study
In this study, the team generated a CFD numerical model considering a few assumptions such as cylinder temperature being consistent with the ambient temperature during the initial injection phase, isotropic heat transfer characteristics of various materials, ignoring the effect of gravity and the exchange of energy among hydrogen and the pipeline connecting the cylinder and the storage tank, and using a two-dimensional (2D) model for the simulation.
The model setting included the application of a 2D pressure solver to the simulation. The accuracy of the results was verified by the storage cylinder’s temperature rise curve with time. The simulation results were validated by comparing them with the experimental data from the existing studies.
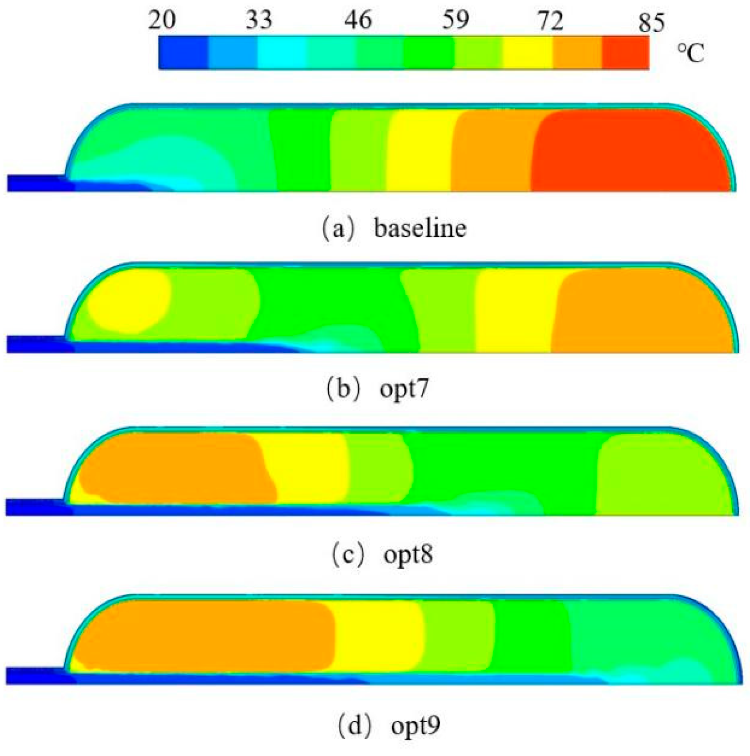
Temperature and velocity contour of hydrogen inside the cylinder at 80 s. Image Credit: Xue, L et al., Energies
Observations
The researchers observed that the rise in temperature within the cylinder can be inhibited by internal cylinder optimization as well as hydrogen injection precooling. The injection can be followed by an increase in the SOC. The highest temperature rise was effectively reduced under six precooling schemes. It was also observed that under several working conditions the temperature distribution within the cylinder was uneven, decreasing from the cylinder’s tail to the mouth. Further, the longer time taken for the hydrogen to flow from the mouth to the tail leads to insufficient convection cooling.
On the other hand, a decrease in the cylinder pressure was observed with a decrease in the injection temperature. Considering a constant filling mass flow rate, the SOC and the filling time increase with a decrease in the inlet temperature. Moreover, upon completion of the injection, the SOC increases with the rise in the injection time and gas temperature reduction. The SOC could further be improved by modifying the cylinder’s internal structure and injection precooling thereby adjusting the temperature uniformity.
The addition of a filling pipe in the cylinder was seen to optimize the heat transfer due to the direct injection of hydrogen while accelerating the internal convective cooling and evening the cylinder’s temperature distribution. The team selected three optimization scenarios at length ratios of 75%, 50%, and 25%, exploring the feasibility of this scheme. The temperature difference in the three scenarios was smaller, while the SOC was higher as compared to the initial scheme. The optimizations increased the SOC by 40.1%, 38.7%, and 16% at length ratios of 75%, 50%, and 25%, respectively.
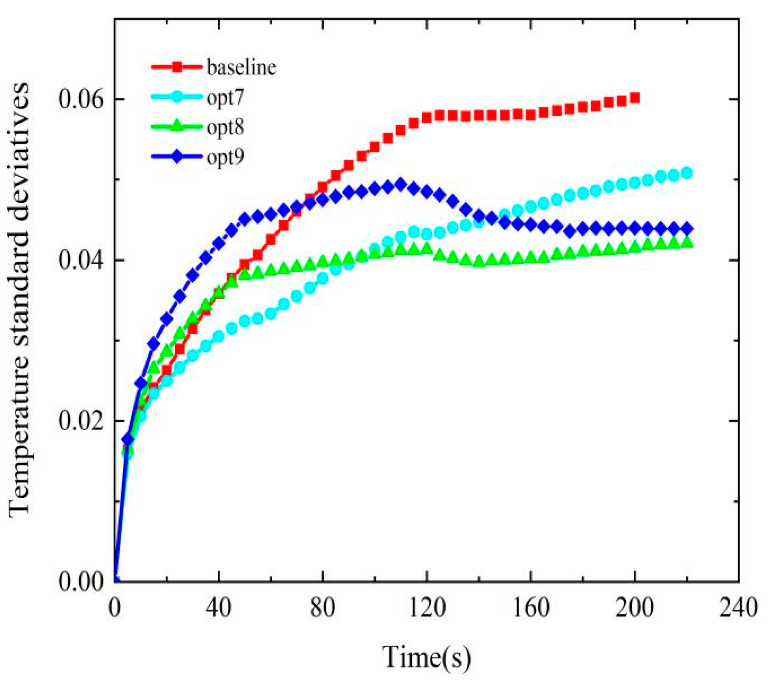
Temperature homogeneity inside the cylinder before and after optimization. Image Credit: Xue, L et al., Energies
Conclusions
To summarize, the researchers used a numerical simulation model to study the effect of hydrogen charging at various temperatures on the pressure, SOC, and temperature rise in the injection process of a 35 Mpa hydrogen storage cylinder. Additionally, the addition of pipelines within the cylinder to improve the SOC was assessed. The pressure increased linearly with an increase in the hydrogen charging temperature as well as charging time.
The precooling treatment of the hydrogen injection leads to a reduction in the maximum cylinder temperature rise and the temperature rise rate. The decrease in the injection temperature gradually increased the SOC up to 49.3%. The precooling of the injected gas was recommended to be -10 °C or lower in consideration of the SOC exceeding 90% and other safety requirements.
Disclaimer: The views expressed here are those of the author expressed in their private capacity and do not necessarily represent the views of AZoM.com Limited T/A AZoNetwork the owner and operator of this website. This disclaimer forms part of the Terms and conditions of use of this website.
Source:
Xue, L.; Deng, J.; Wang, X.; Wang, Z.; Liu, B. Numerical Simulation and Optimization of Rapid Filling of High-Pressure Hydrogen Storage Cylinder. Energies 2022, 15, 5189. https://www.mdpi.com/1996-1073/15/14/5189