By Surbhi JainReviewed by Susha Cheriyedath, M.Sc.Jul 29 2022
In an article recently published in the journal Additive Manufacturing, researchers discussed the utility of laser powder bed fusion (L-PBF) to create an alumina-based ceramic mold with an integrated core and shell (CMCS) for hollow turbine blades.
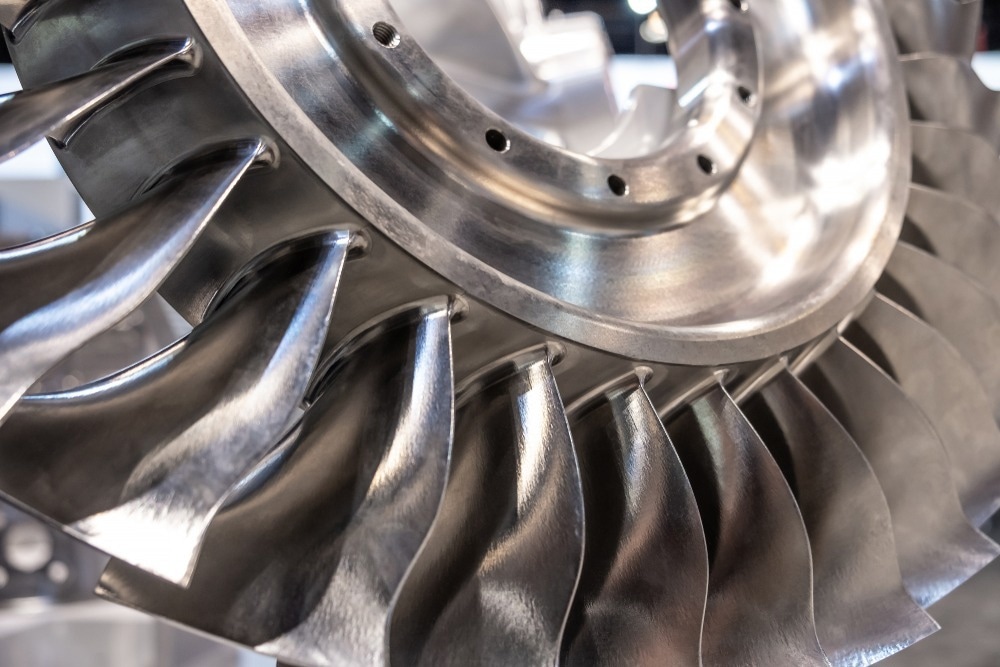
Study: Alumina-based ceramic mold with integral core and shell for hollow turbine blades fabricated by Laser powder bed fusion. Image Credit: Vasyl S/Shutterstock.com
Background
Gas turbine engines' main parts are superalloy turbine blades with elaborate inner cooling tunnels. The precision of the finished turbine blades is greatly influenced by the quality of the ceramic core and shell molds used in investment casting. Alumina-based ceramic is the best substance to use when creating molds.
The yield from the traditional way of creating ceramic molds is unsatisfactory despite the fact that each stage requires lengthy production cycles and expensive costs. The layer-by-layer production of parts with complex structures using additive manufacturing (AM) technology enables the elimination of these challenging and time-consuming processes in the creation of ceramic casting molds.
The preparation of the core and shell are getting more refined as a result of the advancement of ceramic AM technology and related post-treatment technologies. However, the divided ceramic core and shell must be put back together to create a full mold before casting, and the accuracy of the assembly is difficult to manage.
The recommended option in this regard is to produce a CMCS. When compared to the other AM technologies, L-PBF is a great choice for creating big molds with intricate interior structures because no additional support structure is needed during the manufacturing process. Although L-PBF has the ability to construct complicated molds, reports of L-PBF effectively making CMCS are uncommon due to various issues that need to be resolved.
About the Study
In this study, the authors discussed the development of an integral core and shell L-PBF ceramic mold made of alumina. Following a thorough analysis of the effects of the component contents on fluidity and packing density, the optimal formulation for the composite powder was established as 88 wt.% basis points mixed spherical alumina with coarse: fine = 9:1, 0.1 wt.% fumed silica and 12 wt.% epoxy resin E12. After sintering, the mechanical characteristics of alumina ceramic were improved by using the vacuum infiltration procedure, where the solid loading of the ceramic slurry was examined.
The team constructed the CMCS in two components, the core and shell, and the base having a spiral grain selector, which allowed for easier cleaning of leftover powder because of the larger apertures. The divided two portions were joined together by a ceramic binder after the initial infiltration and pre-sintering, and they subsequently underwent a second infiltration and final sintering to produce a full CMCS.
Low sintering shrinkage of 1.51–2.03 %, appropriate apparent porosity of 30.82±0.01 %, and room-temperature strength of 9.72±1.34MPa for bonded specimen and 13.03±2.90 MPa for unbonded specimen, were all characteristics of the alumina-based ceramic made using L-PBF and post-treatment.
The researchers suggested a technique for the direct preparation of CMCS using L-PBF in conjunction with post-treatment infiltration-sintering. The composite powder underwent an optimization study to achieve greater packing and fluidity. The effectiveness of infiltration, as well as the mechanical properties of the alumina-based ceramic, were examined, and the impact of solid loading in the ceramic slurry used for infiltration was also investigated. Further, an alumina-based CMCS manufactured with L-PBF technology was used to create a gas turbine blade.
Observations
The L-PBF-prepared alumina-based material had an acceptable apparent porosity of 30.82% and minimal sintering shrinkage of 1.51 to 2.03 %. The flexural strength of the unbonded specimens was 13.03±2.90 MPa. Flexural strengths of the bonded specimens with flat joint and stepped joint were 8.15±2.67 MPa and 9.72±1.34 MPa, respectively.
The ceramic binder's solid loading was 55% by volume, and the polyvinyl alcohol (PVA) concentration was 3%. The 20 vol.% ceramic slurries had a weight-increasing ratio of 22.24%, which was nearly four times that of the equivalent treated with pure silica sol. The green strengths of E12 at 12%, 9%, and 15% were, respectively, 1.712±0.090 MPa, 1.232±0.208 MPa, and 1.542±0.108 MPa. When fumed silica was added at a rate of 0.1%, the bulk density of the powder increased initially before falling. This value was then maximal at 2.143±0.004 g/cm3. The angle of repose dramatically dropped from 40.577° to 27.288° when 0.1% fumed silica was introduced.
L-PBF created an alumina-based CMCS that had acceptable characteristics and reduced sintering shrinkage, and its viability for casting superalloy turbine blades was successfully confirmed. The optimal composite powder contained 88 wt.% mixed spherical alumina, 0.1 wt.% fumed silica, and 12 wt.% E12. This resulted in a composite powder with a greater packing density and adequate fluidity. The infiltration process and the characteristics of the mold material were significantly influenced by the solid loading of the ceramic slurry.
Due to clogging phenomena and low infiltration efficiency, ceramic slurry with a high solid loading of greater than 25 vol.% was not suitable; instead, ceramic slurry with 20 vol.% was found to be ideal for infiltration.
Conclusions
In conclusion, this study elucidated the production of an alumina-based material with acceptable apparent porosity, minimal sintering shrinkage, and 13.03±2.90 MPa strength at room temperature. The ceramic binder used to link the two components of CMCS had an appropriate strength of 9.72±1.34 MPa, and no visible breaking was discovered at the interface.
The authors mentioned that this study offers a method for producing integral ceramic molds for the superalloy turbine blades utilizing L-PBF technology, an approach that holds promise for producing large and intricate ceramic molds for turbine blades. They also stated that the technique suggested in this study is capable of producing excellent alumina-based CMCSs.
More from AZoM: Reflection Electron Microscopy for Crystal Analysis
Disclaimer: The views expressed here are those of the author expressed in their private capacity and do not necessarily represent the views of AZoM.com Limited T/A AZoNetwork the owner and operator of this website. This disclaimer forms part of the Terms and conditions of use of this website.
Source:
Chen, S., Sun, D., Wang, C., et al. Alumina-based ceramic mold with integral core and shell for hollow turbine blades fabricated by Laser powder bed fusion. Additive Manufacturing 103046 (2022). https://www.sciencedirect.com/science/article/abs/pii/S2214860422004389