A group of researchers recently published a paper in the journal Additive Manufacturing that demonstrated the feasibility of using a proposed hybrid additive manufacturing (AM) technology to fabricate the first fully three-dimensional (3D) printed piezoelectric accelerometer.
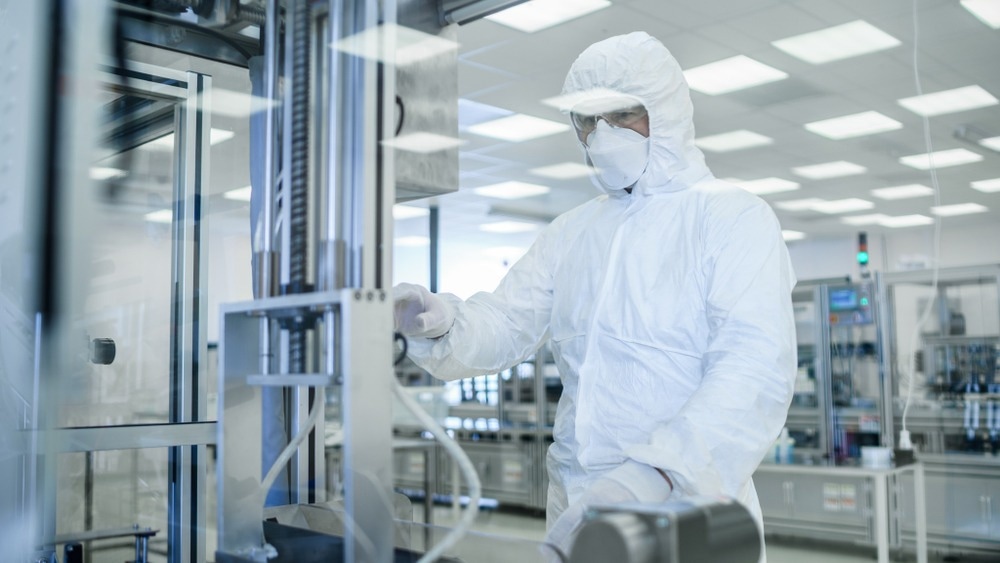
Study: Hybrid Additive Manufacturing of a Piezopolymer-Based Inertial Sensor. Image Credit: Gorodenkoff/Shutterstock.com
Background
AM/3D printing has gained significant attention as a suitable manufacturing methodology for electro-mechanical device fabrication in the past few years due to the enhanced process flexibility, improved product customizability, and better tridimensionality of the mechanical structures prepared using AM techniques.
Electro-mechanical devices, such as accelerometers, are typically composed of electric components with mechanically moveable parts. Thus, the production of such devices is specifically beneficial when various AM technologies, such as stereolithography (SLA) and inkjet printing (IJP), are used in synergy.
For instance, the sensitivity demonstrated by a fully metalized and 3D-printed three-axis or uniaxial accelerometers with differential capacitive sensing was comparable to or better compared to the state-of-the-art micro electro mechanical system (MEMS) accelerometers.
The Study
In this study, researchers fabricated the first fully 3D printed functional accelerometer capable of piezoelectric signal readout using a new hybrid AM technology, which combined SLA and IJP techniques and experimentally verified the fabricated device.
SLA was used to print the structural components of the uniaxial accelerometers using the photocurable THERMA DM500 resin, while IJP was employed to fabricate the piezoelectric readout part by depositing a polyvinylidene fluoride-trifluoroethylene (PVDF-TrFE) piezoelectric layer and the corresponding conductive silver electrodes (silver/P(VDF-TrFE)/silver) on the SLA-printed device surface.
THERMA DM500 commercial resin was selected to print the structural parts of the accelerometers due to its high glass transition and thermal degradation temperatures, which were necessary considering that high temperatures were used for annealing the functional P(VDF-TrFE) layer and silver electrodes. Corona treatment was used to increase the hydrophilicity of the resin surface.
IJP, an efficient and scalable deposition technology, was selected for the deposition of functional layers as it offered a costless, facile, and reproducible patterning technique to fabricate the piezoelectric material and the corresponding interconnections. COMSOL Multiphysics version 5.6 was used to perform finite element analysis (FEA) to confirm the reliability of the experimental measurements.
All structural parts and samples were printed with a commercial SLA machine, model 028J Plus, while a Dimatix DMP-2850 with a 10 pL cartridge was employed to inkjet print the bottom and top electrodes and the piezoelectric polymer on the substrate. During IJP, plate temperature was set to its maximum value of 60 °C to prevent the coffee-ring effect and ensure a faster printing process.
Both bottom and top electrodes were cured for one hour and a half at 130 °C after deposition. 0.7% pure solid P(VDF-TrFE) was dissolved in a mixture containing 70% wt. dimethyl sulfoxide (DMSO)/ 30% wt. methylethyl ketone (MEK) to obtain an optimal droplet ejection during the piezoelectric polymer layer printing.
1.5 kHz jetting frequency, 35 V printing voltage, and a 45 °C nozzle temperature were maintained to print the piezopolymer layers. Subsequently, the P(VDF-TrFE) layer was annealed at 140 °C for two hours. Fully 3D printed accelerometers were mounted on a shaker along with a reference accelerometer for characterization.
To assess the shrinkage of the printed structures over time, the volumes of cubic samples were determined immediately after printing, after post-curing, and subsequently at specific intervals of time. The shrinkage values of the resin in terms of thickness were then obtained by printing and measuring several beams with different thicknesses and widths.
Observations
Two 3D uniaxial accelerometers, designated as geometry B and geometry A, were efficiently manufactured using the SLA technique. The mass suspension mechanisms of the two designs differed from each other. Finite element method (FEM) modeling guided the accelerometer design and fabrication processes.
Geometry A was composed of a proof mass of 8 mm x 11 mm x 4 mm and was suspended using two elongated bottom and top springs of 7 mm x 11 mm x 345 µm. An anchor with 17 mm x 10 mm x 6 mm dimensions provided the connection between the fixed substrate and the springs.
The piezoelectric sensing element containing two silver electrodes and a P(VDF-TrFE) layer was deposited using IJP on the wide and flat upper face of the top spring, hosted, and annealed at high temperatures to obtain the first fully 3D printed piezoelectric accelerometer.
The accelerometer deformed based on its first flexural mode, and a voltage signal was generated in the piezopolymer, which was detected to determine the external acceleration that acted on the accelerometer.
Similarly, geometry B was composed of a proof mass of 11 mm x 8 mm x 2 mm and was suspended through two elongated right and left springs of 7 mm x 11 mm x 345 µm.
Two anchors of 19 mm x 7 mm x 6 mm dimensions were used to connect two springs to a fixed substrate. The sensing element was deposited on the top faces of the springs, and the external acceleration was determined in a similar manner as geometry A.
The P(VDF-TrFE) layer displayed an effective piezoelectric behavior after annealing and poling. 50 P(VDF-TrFE) layers were deposited to prepare a five µm thick continuous and pin-hole-free P(VDF-TrFE) film to ensure full insulation between the top and bottom electrodes to prevent short circuits.
Supports were introduced during the SLA printing process and kept till the end of the IJP process to provide mechanical support to prevent uncontrolled deflection of the polymeric structure, which was attributed to the annealing performed to cure the functional layers and maximum plate temperature.
The surface roughness of the vertically printed resin samples using SLA was higher compared to the horizontally printed samples, which necessitated the deposition of multiple silver layers to completely cover the resin surface.
Although two silver layers were sufficient for resin surface coverage, three layers were deposited to achieve a bottom silver electrode with extra thickness. After silver deposition, the resin surface was mildly leveled. The thickness of the top silver electrode was kept smaller compared to the piezoelectric layer and bottom electrode to avoid short circuits.
A highly hydrophilic resin surface was obtained after corona treatment to prevent pattern breakage. Specifically, the silver ink distribution was notably better on the treated resin sample surface with high wettability as the surface limited the local accumulation of the ink material and reduced the chances of developing micro-cracks.
The droplet speed and the jetting frequency during the IJP of silver nanoparticle ink were set at six m s-1 and five kHz, respectively, to ensure total resin coverage, optimize layer uniformity, maximize pattern precision, and minimize printing time.
Shrinkage of the printed structures was mostly observed during the 30 min post-curing process and the average shrinkage was 3.76% after the post-curing process. Moreover, the shrinkage values were larger for beams with a smaller width.
In the geometry A accelerometer, a considerable discrepancy was observed between the natural frequency values obtained from experiments and numerical predictions for external accelerations of 5 g and 1.8 g, which was attributed to the uncertainties in material properties and geometry.
However, the natural frequency values of the geometry B accelerometer estimated through a modal analysis were in good agreement with the values obtained from experiments even after considering fabrication imperfections and material properties uncertainties.
The sensitivity of both devices was one order of magnitude below the numerical predictions made by COMSOL Multiphysics v.5.6, as the electric field value used in the polling stage was much lower than the prescribed limit due to fabrication process-induced limitations.
To summarize, the findings of this study effectively demonstrated the ability of the 3D printed piezoelectric accelerometers to sense acceleration and the feasibility of using the proposed hybrid AM technology to fabricate electro-mechanical sensors at the mesoscale.
More from AZoM: What is Glow Discharge Optical Emission Spectrometry
Disclaimer: The views expressed here are those of the author expressed in their private capacity and do not necessarily represent the views of AZoM.com Limited T/A AZoNetwork the owner and operator of this website. This disclaimer forms part of the Terms and conditions of use of this website.
Source:
Levi, M., Zega, V., Hatami, D. et al. Hybrid Additive Manufacturing of a Piezopolymer-Based Inertial Sensor. Additive Manufacturing 2022. https://www.sciencedirect.com/science/article/pii/S221486042200481X?via%3Dihub