In a paper recently published in the journal Advanced Materials Technologies, researchers established a 3D printing method based on extrusion to produce iron- and steel-based structures with extremely high porosity with three hierarchical-level distributions.
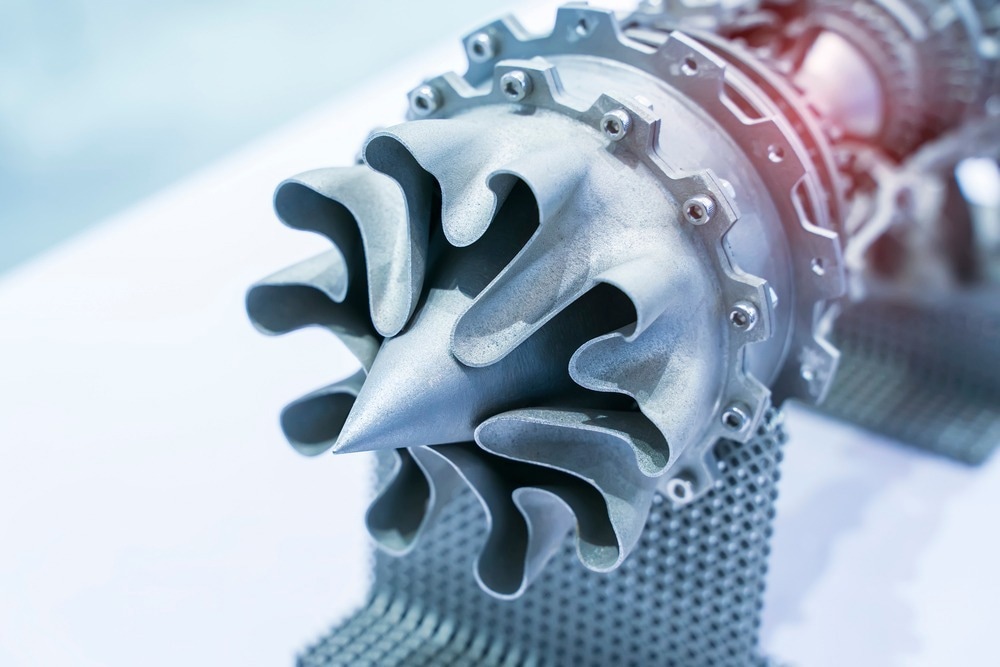
Study: 3D Printing of Hierarchical Porous Steel and Iron-Based Materials. Image Credit: asharkyu/Shutterstock.com
Background
Porous metals find their usage in filters, battery components, and filters and have lately been evaluated for catalysis, lightweight construction, tissue regeneration, and thermal management. Controlling the structure's pore size and porosity enables tailoring the porous metal's characteristics to fit the needs of certain applications.
Powder bed fusion, direct ink writing (DIW), and electron beam melting are among the methods of 3D printing used to create cellular and porous metals. DIW is particularly appealing since it allows for the printing of complicated structures utilizing low-cost and readily accessible desktop printers at room temperature. DIW's potential as a method for manufacturing metals with customizable hierarchical porosity structures has yet to be completely realized. Moreover, the use of emulsion inks and foam to build hierarchical porous metals is an appealing method that has yet to be explored.
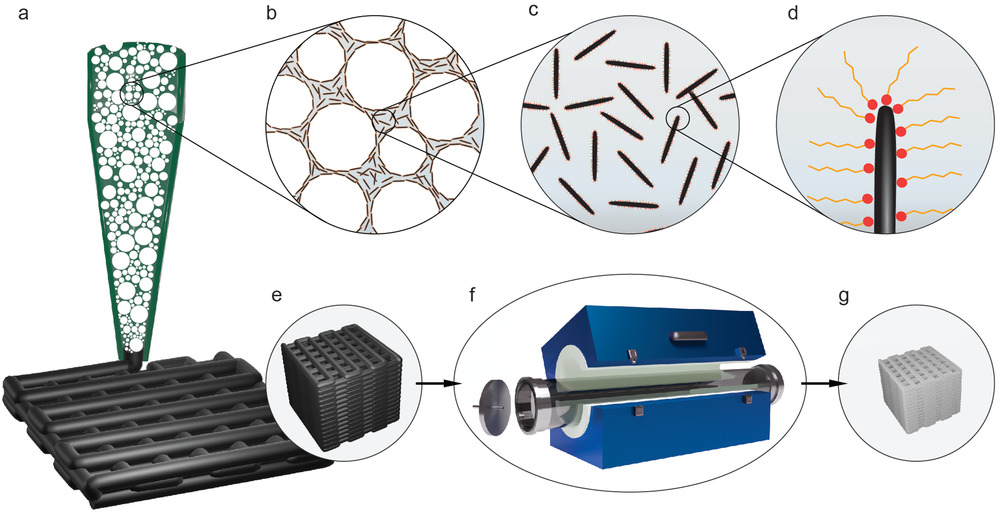
Schematic of the manufacturing process of iron-based hierarchical porous structures. a–d) Direct ink writing (a) of closed-pore, particle-stabilized wet foam (b) made by frothing a suspension of magnetite microrods (c) functionalized with a short-chain amphiphilic molecule (d). e) The as-printed structure is reduced and sintered in a tubular oven under f) constant H2 gas flow to g) an iron-based open porous structure. Image Credit: Carpenter, J. A et al., Advanced Materials Technology
About the Study
In the present study, the team developed and studied a DIW approach for the fabrication of hierarchical porous iron- and steel-based metals employing particle-stabilized foams that functioned as self-assembling inks. Ball-milling was used to homogenize an aqueous solution containing hexylamine and 40-50 wt% metal oxide powder. An electrical stirrer was then used to foam the slurry. The resultant foam was then volumetrically printed.
Furthermore, sample reduction was carried out in a quartz tube oven. H eating of the specimens at 1000, 650, or 650 °C caused the oxidization of the as-printed magnetite foams into various oxide phases. Hydrophobic-fumed silica in hexane suspension was used to dip-coat the samples to hydrophobize the hierarchical porous structures, followed by drying. A scanning electron microscope was used to capture high-resolution photographs before and after foam reduction. A powder diffractometer was used to acquire X-ray diffraction patterns.
Additionally, universal mechanical testing equipment was used to determine the modulus and compressive strength. The hydrophobized porous iron structure's ability to absorb oil was tested by exposing a water-floating sample to hexane as an absorbent. By compressing the specimen between copper tape followed by the application of electrical current using a power supply from the laboratory, the resistive heating properties of partly oxidized porous iron structures were tested.
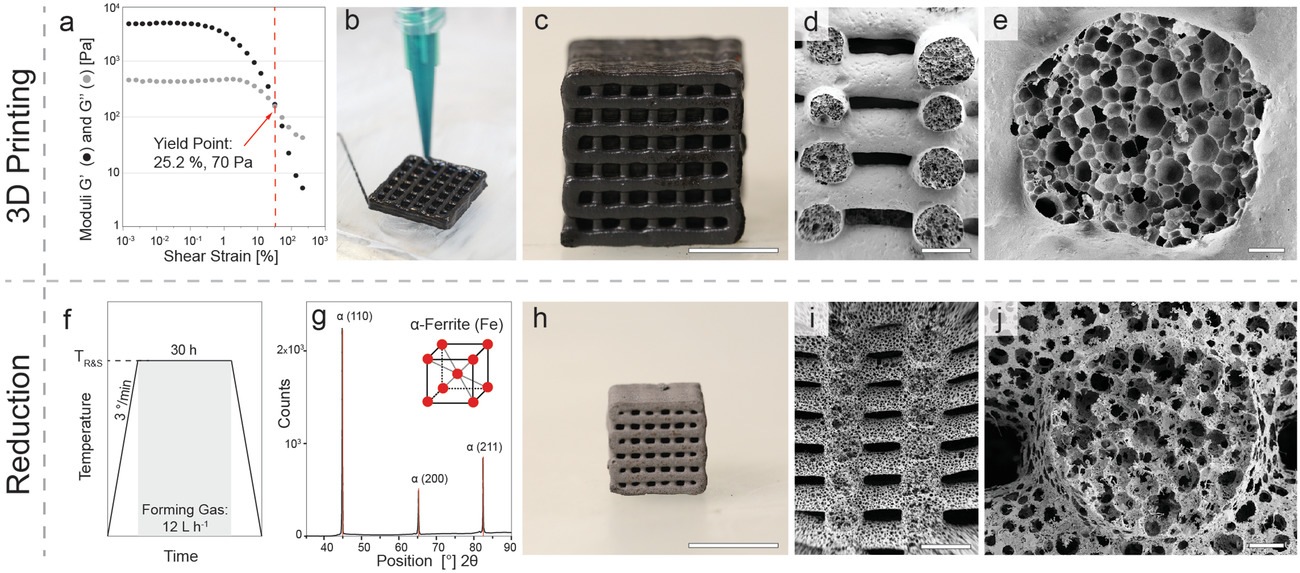
3D printing and reduction of foams to generate iron-based hierarchical porous structures. a) Strain-controlled oscillatory rheology performed to quantify the viscoelastic properties of the wet foam with optimum concentrations of surface modifier (3 µL g−1) and iron oxide particles (50 wt%). b) Direct ink writing of the stable foam using a desktop extrusion-based printer equipped with a syringe and nozzle size of 0.84 mm. c) Optical and d,e) SEM images of the printed stable foam after drying. f) Typical heating protocol used for the reduction and sintering of dried foams. In this representative example, the foam is treated at 850 °C for 30 h. g) XRD pattern of the fully reduced sample and its clear correlation with the diffraction peaks expected for a ferritic (α-Fe) atomic structure. h) Optical and i,j) SEM images of the reduced sample. Scale bars indicate 1 cm (c,h), 1 mm (d,i), and 100 µm (e,j). Image Credit: Carpenter, J. A et al., Advanced Materials Technology
Observations
It was found that functionalizing the magnetite particles with hexylamine offered the optimal wettability to facilitate adsorption at the interface between air and water, resulting in stable, strong foams upon the incorporation of air. a distinct viscoelastic response, including a low-stress storage modulus plateau and a clearly defined yield stress. The foams showed a 4.86 kPa high plateau storage modulus, making them rigid enough for direct ink printing of grid-like designs. The team further determined that the particle-stabilized wet foams' excellent viscoelastic nature and stability mitigated any compressibility concerns under normal printing circumstances.
The treated sample's XRD patterns demonstrated that the original magnetite had been completely reduced to ferritic iron. The combined sintering and reduction process resulted in a 50% linear shrinkage followed by the formed closed-celled macropores being opened during foaming. As a result, a distinct, porous, open-celled structure with three hierarchical porosity levels was formed. It was determined from the microstructural investigations that avoiding high temperatures is necessary to preserve the three-level hierarchical porosity as well as a high carbon content. Moreover, mechanical characterization revealed that the inclusion of nickel significantly increased the compressive strength and elastic modulus of the porous iron-based alloys.
The intrinsic magnetic and significant electrical conductivity observed for iron was found in the porous metal structures themselves, which can be printed into a variety of large-scale designs. Additionally, the structure's extremely low density made it light enough for them to float on water. Therefore, the porous structures from the present study can be utilized as oil absorbents that are environmentally friendly. The structures' density rises as oil replaces air in the channels and pores until they begin to sink. This might make it possible to confine crude oil spills before being transported back to the sea floor. These materials can potentially be employed as low-power resistive evaporators since they have higher electrical resistivity than their pure iron equivalents.
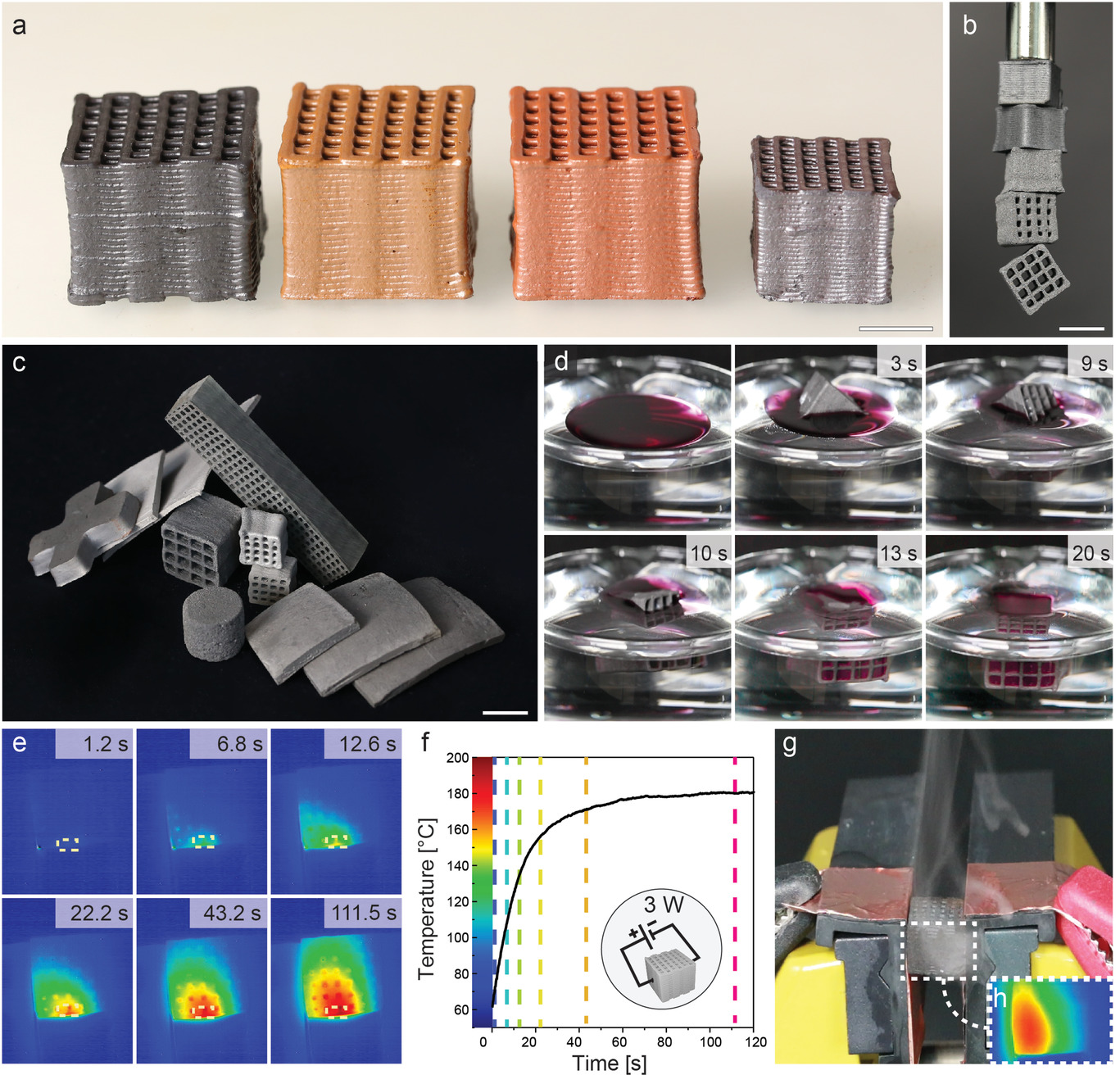
Possible applications of iron-based hierarchical porous structures. a) Lightweight, permeable, and high-surface-area structures with tailored chemical compositions (from right to left): unreduced magnetite foam, maghemite foam obtained upon oxidation of magnetite at 550 °C for 2 h (brown), 37 wt% maghemite and 63 wt% hematite foam obtained upon oxidation of magnetite at 650 °C for 2 h (red), sintered hematite foam obtained by sintering at 1000 °C for 2 h (silver). b) Iron-based foams attracted to a macroscopic magnet. c) Selection of 3D-printed and molded iron foams. d) Hydrophobized iron foam absorbs colored oil quickly and selectively off a water bath. Because it wets the surface of the foam, the oil is contained within the micro- and macropores of the structure. e–g) Resistive heating of iron-based foams for the on-demand vaporization of liquids: (e) time-lapsed infrared images of a 35% Fe foam (5.6 Ω at room temperature) subjected to an electric voltage at 3 W power. The average temperature profile of the area marked in (e) is displayed in (f). The time points of the snapshots in e) are indicated with dashed lines in (f). g) Optical and h) thermal images show on-demand liquid evaporation via resistive heating using a foam infused with etheric oil (limonene, 0.4 mL g −1). Scale bars denote 1 cm. Image Credit: Carpenter, J. A et al., Advanced Materials Technology
Conclusions
To summarize, the study showed that it was possible to produce ultralight steel as well as iron-based materials having up to three hierarchical porosity levels via DIW using particle-stabilized foams. In order to maintain the structure's macropores while adding microporosity to the solid metallic phase, the temperature and time of the reduction process proved critical.
The reduced relative density observed for the structure did not affect the porous metal’s mechanical effectiveness since the overall porosity was dispersed over multiple length scales. According to the authors, the hierarchical porous metals produced in this research can be adequately light enough to float in water for oil spill absorption. With a widely sustainable and accessible mineral resource, this manufacturing method provides a strong foundation for producing lightweight and practical materials.
Disclaimer: The views expressed here are those of the author expressed in their private capacity and do not necessarily represent the views of AZoM.com Limited T/A AZoNetwork the owner and operator of this website. This disclaimer forms part of the Terms and conditions of use of this website.
Source:
Carpenter, J. A., Passaleva, N., Häring, M., Mikl, G., Studart, A. R., 3D Printing of Hierarchical Porous Steel and Iron-Based Materials. Adv. Mater. Technol. 2022, 2200971. https://doi.org/10.1002/admt.202200971