By Surbhi JainReviewed by Susha Cheriyedath, M.Sc.Nov 14 2022
In an article recently published in the open-access journal Scientific Reports, researchers discussed the development, design, and utility of a self-spiraling pattern-driven 4D-printed actuator.
Study: Design, fabrication and application of self-spiraling pattern-driven 4D-printed actuator. Image Credit: S.Gvozd/Shutterstock.com
Background
In nature, self-spiraling structures are common. The bounds and meanings of conventional 3D printing have been broadened with the advent of the 4D printing concept, making it possible to fabricate many intricate structures.
Due to years of study on intelligent materials and structure design, there are numerous ways to induce 3D shape changes in printed actuators in the temporal dimension. The expected deformation is produced by 4D printing via the stimulation process of smart materials. To adjust the distribution of stress-strain during deformation and subsequently control the deformation, 4D printing also makes use of printed actuator designs.
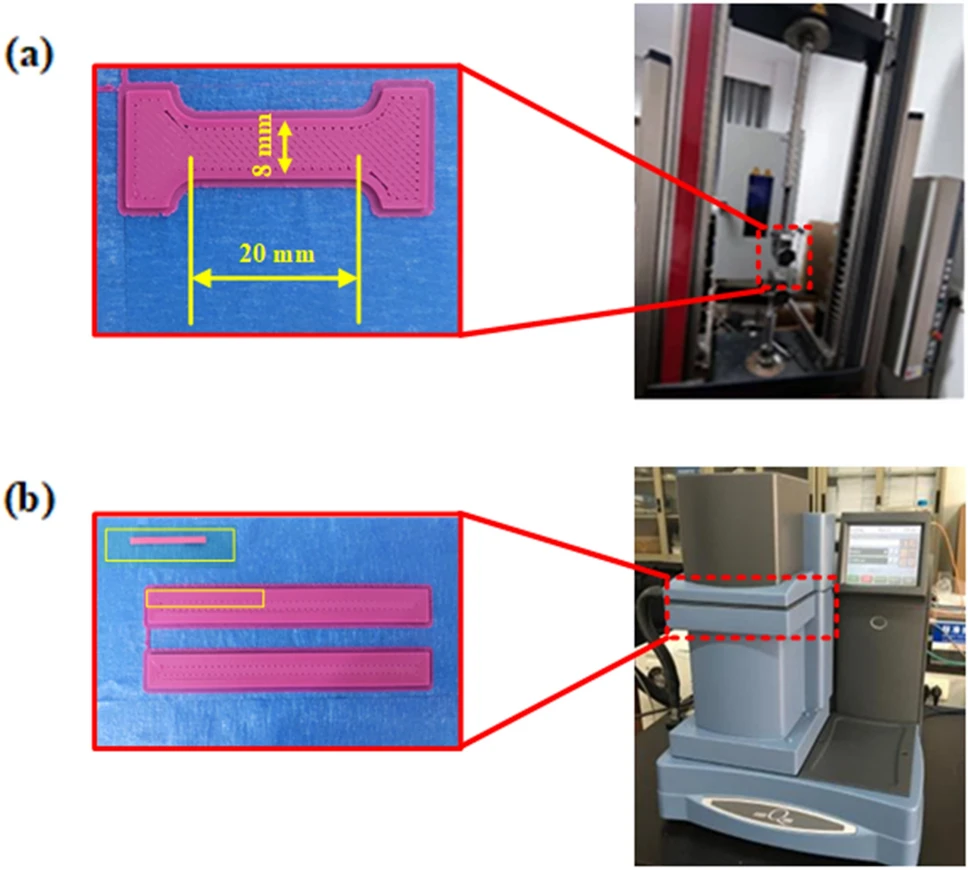
(a) DMA machine and printed sample; (b) tensile machine and printed sample. Image Credit: Zeng, S et al., Scientific Reports
According to earlier research, the shape-memory characteristics of the structures are influenced by the process parameters in different printing forms. The trends and effects of printing parameters on mechanical properties vary for various specific configurations of the same material.
There is currently minimal research on these problems for self-spiraling structures made with 4D printing. To offer direction in the design of mechanical properties, simulation models must be created in addition to experimental studies. The intrinsic relationship between mechanical properties and printing parameters needs to be further studied.
About the Study
In this study, the authors used both experimental and theoretical techniques to examine the stimulus effects of fiber patterns and fabrication factors on the self-spiraling behaviors of the bilayer actuator. Pattern design recommendations were provided for 4D-printed self-spiraling actuators to satisfy various application needs. This study intended to methodically examine the structural layout and deformation process of 4D-printed controlled self-spiraling actuators.
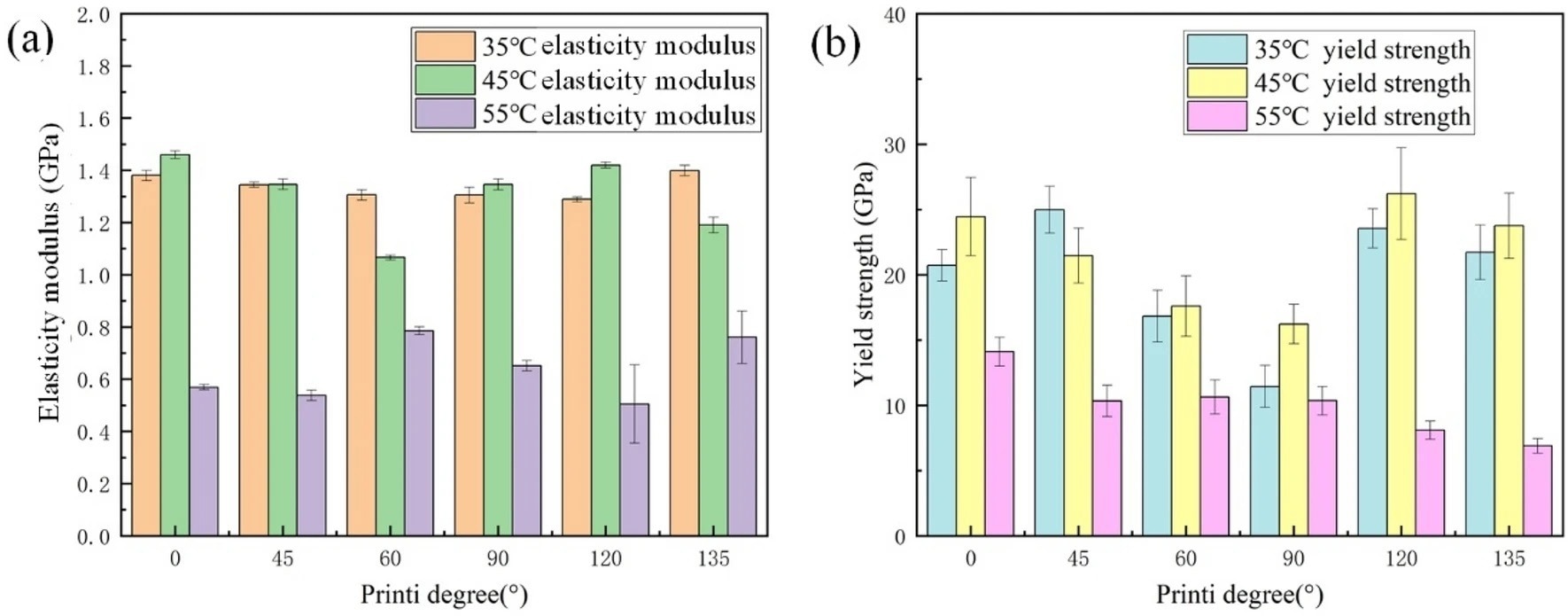
(a) Elasticity modulus for each temperature workpiece; and (b) yield strength of the workpiece at each temperature. Image Credit: Zeng, S et al., Scientific Reports
The team proposed a simulation parameter model after analyzing the deformation process of a controllable and self-spiraling actuator using a thermodynamic intrinsic model. The rule of change governing the deformation of the elastic modulus was discovered through the design of thermal excitation experiments. In addition, a shape memory performance index was presented to examine the effects of various printing temperatures, to adjust the thermodynamic model's variables, and to offer recommendations on the choice of printing parameters.
The researchers used COMSOL to simulate self-spiraling brakes with various printing angles at the ideal printing temperature and compared the results to the experimental fiber. Further, a self-spiraling actuator was used to accomplish a self-assembly process for the self-spiraling structure based on the simulation model.
Observations
While a printing angle of 30 °C offered a superior pitch-to-self-spiraling radius ratio, a printing temperature of 200 °C offered better shape and performance. The self-spiraling structure from the simulation was favored in the vertical printing plane when the printing angle was between 90° and 180°, and the pitch decreased as the angle increased. The self-spiraling structure’s pitch produced by simulation was 0° when the angle with printing was 0° and 180°, and the deformation of the bilayer actuator was 90°.
The glass transition temperature trend caused the temperature to increase in fiber at 210 °C. At 200 °C, Rf achieved its maximum value of 0.4 before falling to 0.127 and then increased once more to 0.25 at 210 °C. The best shape memory performance was achieved at a printing temperature of 200 °C, as indicated by the comprehensive performance, where the R-value reached a maximum value of 0.3.
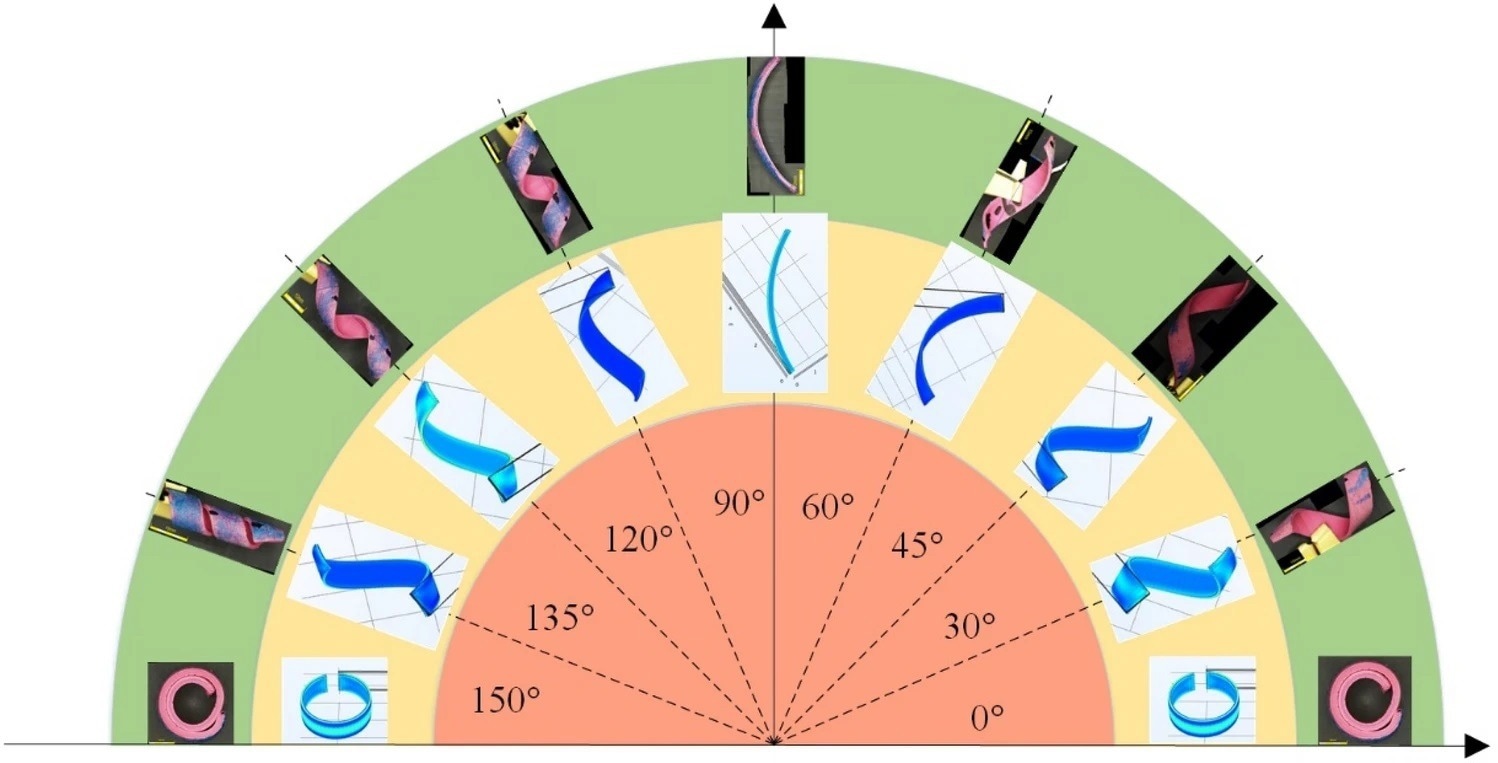
Simulation and experiment for different printing angles. Image Credit: Zeng, S et al., Scientific Reports
With a rise in printing temperature, the storage modulus' maximum value in the low-temperature area declined and reached a minimum value of 1324 MPa at 205 °C. In the four experimental groups, the Tg values were 70.7, 76.72,71.63, and 76.82 °C. The yield strength of PLA print samples with 120° and 135° printing angles was higher at 35 and 45 °C than that of 60° and 45 °C, and at 55 °C it was higher yet for samples with 60° and 45° printing angles than for those with 120° and 135°.
The elastic modulus of the polylactic acid (PLA) printed strips gradually decreased as the surrounding temperature increased, from an average elastic modulus of 1.3373 GPa at 35 °C to an average elastic modulus of 0.635 GPa at 55 °C, and finally to an average elastic elasticity of 0.004 GPa at 70 °C.
Conclusions
In conclusion, this study investigated how self-spiraling structures created via 4D printing behave mechanically. A shape memory polymer bilayer actuator-based fused deposition modeling (FDM) printing technique was designed, experimentally examined, and simulated, with particular attention paid to the printing temperature and printing angle.
The outcomes demonstrated that the printing angle impacted both the elastic modulus and the deformation trend in 4D printing. Shape memory behavior was imposed throughout the self-jet nozzle's extrusion operation. The best shape memory performance was at a printing temperature of 200 °C.
Based on the pre-processing experimental simulation, the authors performed a self-assembly experiment utilizing a self-spiraling brake.
The team mentioned that this study would clarify the multifunctional structural design and simulation of self-spiraling structures and aid researchers in better understanding the effects of 4D-printed microstructures.
References
Zeng, S., Gao, Y., Qiu, H., et al. (2022) Design, fabrication and application of self-spiraling pattern-driven 4D-printed actuator. Scientific Reports 12, p. 18874. https://www.nature.com/articles/s41598-022-23425-0
Disclaimer: The views expressed here are those of the author expressed in their private capacity and do not necessarily represent the views of AZoM.com Limited T/A AZoNetwork the owner and operator of this website. This disclaimer forms part of the Terms and conditions of use of this website.