A recent article published in the Journal of Manufacturing and Materials Processing detailed the synthesis of SiC-Ti3AlC2 and TiC-Ti3AlC2 composites using the fused granules fabrication (FGF) method.
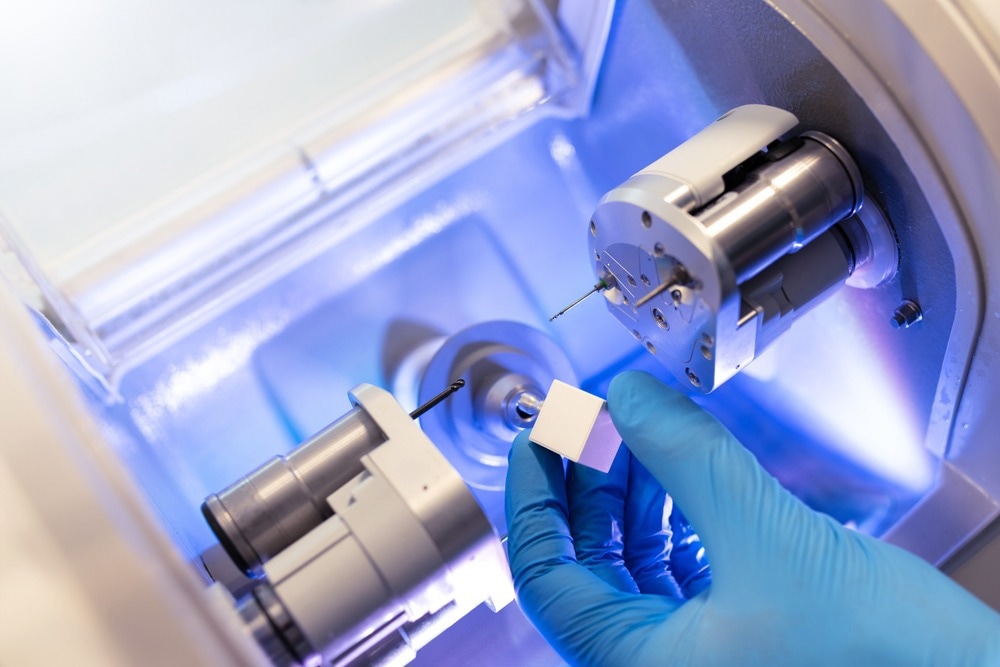
Image Credit: Yalcin Sonat/Shutterstock.com
Background
Ceramic composites offer excellent high-temperature stability, low thermal expansion coefficients, high hardness, wear resistance, and other properties.
Among these, TiC-based ceramics are prominent in industries such as aviation and space due to their high-temperature structural properties. Alternatively, SiC-based ceramics are used as high-temperature heating elements and in tribological applications. Additionally, porous SiC- and TiC-based materials are useful for filtration, separation, catalytic reactions, and hydrogen storage.
With their unique combination of metal and ceramic properties, MAX phases are often added to ceramic composites to enhance high-temperature stability. These phases, represented by the formula Mn+1AXn (where M is an early transition metal, A is a group element, and X is C/N), include ternary carbides and nitrides.
This study investigated SiC-Ti3AlC2 (TAC:SiC) and TiC-Ti3AlC2 (TAC:TiC) composites produced by the FGF method, a material extrusion additive manufacturing (MEAM) technology used to obtain high-quality samples from ceramic materials.
Methods
For fabricating the ceramic composites, mixtures of TAC:SiC and TAC:TiC powders were used in different volume ratios (70:30, 50:50, 30:70). These powders were mixed by a dry method to prepare feedstock for FGF and spark plasma sintering (SPS). Additionally, MC2162 polymer binder (a mix of polyester and polyamide with a mass ratio of 1:5) was used to prepare the feedstock.
The premixed material was extruded in a single-screw extruder at 145 °C to obtain a homogeneous feedstock. The feedstock's rheological properties were characterized using a plastometer and capillary rheometer to determine the melt flow index and viscometry.
Bulk ceramic samples were produced using both FGF and SPS methods for comparison. The FGF process employed a three-dimensional (3D) printer with a custom screw-based pellet-fed printing head to produce bulk samples of size 20×5×5 mm3, followed by sintering.
The 3D printing parameters, such as extrusion coefficient and de-binding speed, were thoroughly optimized. Alternatively, SPS was performed for five minutes at 1200, 1250, and 1300 °C at 50 MPa to produce cylindrical samples of six grams each.
All ceramic samples were studied using optical metallography and scanning electron microscopy (SEM). Additionally, their phase composition was determined using an X-Ray diffractometer (XRD). The three-point bending test and microhardness measurements (Vickers method) were performed to examine the mechanical properties of the fabricated ceramic composites.
Results and Discussion
Optimization of the additive formation parameters resulted in the successful synthesis of ceramic composites. SEM images revealed no macro-defects or cracks in FGF samples, indicating proper printing modes and de-binding processes.
Micron SiC particles with submicron TiC satellites and micron TAC particles represent the overall microstructure of the composites. While the SiC particles form the main skeleton, TAC and its decomposition products were positioned along the boundaries of the skeleton particles, thereby increasing the composite’s strength.
Submicron-sized elements were observed in FGF TiC:TAC samples after sintering.
Submicron pores were also visible on the fracture and cross-section. Sintering decomposed TAC into TiC and Al while releasing tin, which acted as an additive suppressing the growth of the Ti2AlC phase during Ti3AlC2 synthesis. Thus, the TiC:TAC structure mainly comprised TiC and preserved particles of the MAX phase.
Alternatively, the SPS samples retained a greater MAX phase, as evidenced by their fracture surfaces. These samples also exhibited a high density compared to the porous structure of FGF samples.
For samples with the same composition of SiC:TAC (70:30) sintered at 1300 °C, the hardness of the SPS samples was 290 ± 15 HV(0.5/10), while that of the FGF samples was 89 ± 5 HV(0.5/10). The porosity and phase composition of the samples were responsible for this difference in hardness.
The sintering temperature was observed to significantly influence the composite strength, greater than the porosity. Thus, TAC in this study could be considered an additional factor in adjusting the porosity in addition to the main factors of sintering temperature and polymer content in the feedstock.
Conclusion
The study examined ceramic composites with various component ratios and powder/polymer compositions. By optimizing FGF parameters, the researchers successfully synthesized TiC and SiC composites without macroscopic defects.
The optimal de-binding time for samples with a 5×55×5 mm cross-section was 84 hours, sufficient to remove 99 % polymer. The best mechanical properties were achieved at a sintering temperature of 1300 °C for both TiC and SiC composites.
Key parameters regulating porosity in FGF samples included TAC content, sintering temperature, and polymer content.
Journal Reference
Krinitcyn, M., Kopytov, G., Ryumin, E. (2024). Additive Manufacturing of Ti3AlC2/TiC and Ti3AlC2/SiC Ceramics Using the Fused Granules Fabrication Technique. Journal of Manufacturing and Materials Processing. doi.org/10.3390/jmmp8030123
Disclaimer: The views expressed here are those of the author expressed in their private capacity and do not necessarily represent the views of AZoM.com Limited T/A AZoNetwork the owner and operator of this website. This disclaimer forms part of the Terms and conditions of use of this website.