One of the leading suppliers of corrosion resistant refractory metals, H.C. Starck Solutions provides engineered material solutions for a wide spectrum of industries where corrosion resistance is important for enhanced performance. Some of the applications include cladding for vessels, tubing for heat exchangers, and linings for piping.
Corrosion Resistant Refractory Metals
Corrosion resistant refractory metals include tungsten, tantalum, niobium and molybdenum. Corrosion resistant tantalum alloys have been employed in a wide range of process industries where aggressive and hazardous chemicals are used. Tantalum alloys are cost-effective and help extend the service life of major components used in harsh corrosive environments.
ULTRA 76: New Tantalum Alloy
.jpg)
Figure 1. ULTRA 76 alloy
ULTRA 76, the new tantalum alloy from H.C. Starck Solutions, has enhanced corrosion resistance in sulfuric and hydrochloric acids applications utilizing higher concentrations and temperatures. Furthermore, hydrogen embrittlement is reduced since hydrogen pickup is reduced by two magnitudes over typical NRC 76 material with up to 10 times lower in sulfuric acid and 100 times lower in hydrochloric acid.
A robust alloy is required for corrosion applications where improved corrosion resistance in hydrochloric and sulfuric acids, as well as the physical properties of tantalum are preferred at a higher strength level.
Applications of ULTRA 76
The ULTRA 76 alloy is used in a variety of applications. Some of the applications include:
- Heat exchangers, condensers and coils
- Bayonet heaters, single and multi-tube types for use in steam heating in corrosive atmospheres
- Thermocouple protection sheaths, loose line or machined from solid
- Paddle stirrers and agitators, solid or covered (loose-lined)
- Pumps, bodies or cases, shafts and impellers for corrosive chemical solutions
- Tantalum clad dip pipes, heaters and chemical plant equipment
- Distillation columns, boilers and condensers
- Furnaces and furnace parts, for use at temperatures up to 1371°C (2500°F) in controlled atmospheres
- Crucibles in both standard and unique shapes and sizes
- Repair kits for vats, tanks, and other glass-lined containers
Conclusion
There is a possibility for high operating temperatures in sulfuric and hydrochloric acids and at the same time should allow easy fabrication, eliminate complex repairs and production losses, and ensure a reliable and extended service life. When compared to alternative materials, ULTRA 76 enables operations in challenging environments, reduces downtime, and helps in prolonging the life of the equipment. The alloy also removes the requirement for ‘Platinum Spot welding’ application steps to guard against hydrogen embrittlement, and preserves the mechanical characteristics of NRC 76 material.
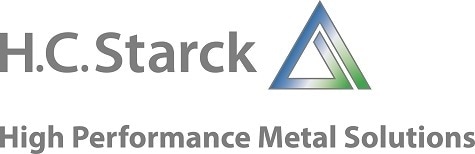
This information has been sourced, reviewed and adapted from materials provided by H.C. Starck Solutions.
For more information on this source, please visit H.C. Starck Solutions.