By Owais AliReviewed by Lexie CornerMar 27 2024
Steel's widespread industrial adoption is attributed to its desirable properties of strength, toughness, machinability, and cost-effectiveness. However, its susceptibility to corrosion results in substantial economic losses, with estimates suggesting that 25 to 33 % of annual steel production is lost to corrosion during service life.1
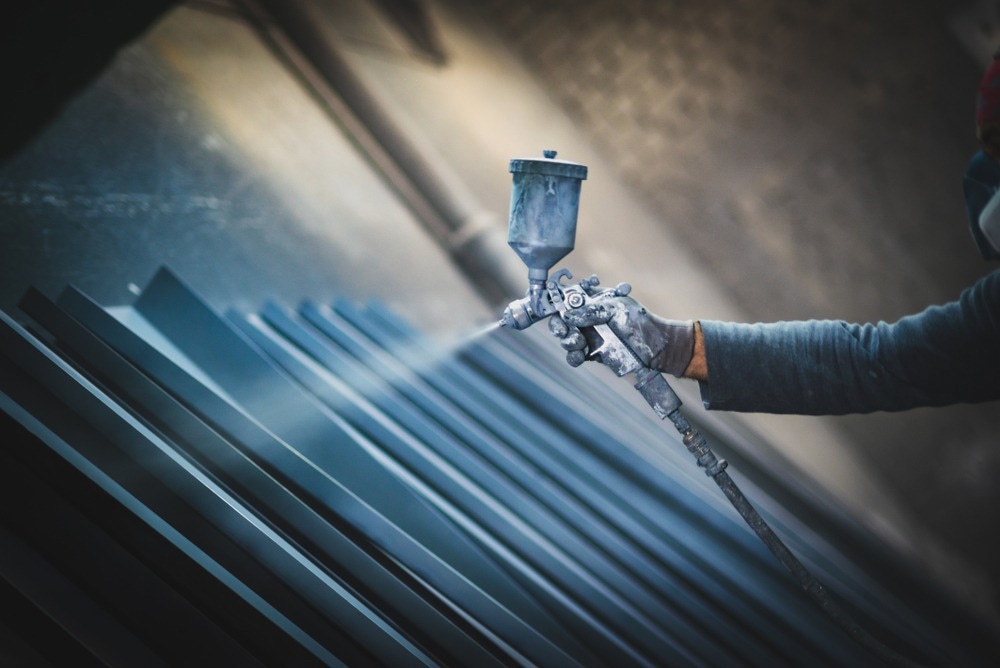
Image Credit: Dizfoto/Shutterstock.com
While traditional methods like painting and hot-dip galvanization have been widely adopted, the persistent pursuit of innovation has driven the development of advanced surface treatment technologies. These cutting-edge techniques deliver superior corrosion protection and enhanced durability while enabling precise, targeted treatment without compromising overall structural integrity or performance.
The Significance of Surface Treatments for Steel Corrosion
Corrosion occurs when steel undergoes an electrochemical process, during which electrons are transferred from the metal to an oxidizing agent, resulting in the formation of rust or other corrosion products.
Enhancing the steel's corrosion resistance ensures its longevity in various applications. This not only brings about notable economic benefits by lowering repair expenses and the need for frequent replacements due to corrosion-related problems but also strengthens safety measures by reducing the likelihood of structural failures and equipment malfunctions. Improving corrosion resistance also prolongs service life, decreases energy consumption, and helps protect the environment.
Advanced surface treatments offer a promising solution by preventing the initiation and propagation of corrosion. These treatments may involve forming protective layers, altering the chemical composition, or inducing microstructural changes that enhance the material's resistance to corrosive environments.2
Advanced Surface Treatment Techniques
Hot-Dip Galvanization
Hot-dip galvanization (HDG) is a well-established and widely employed surface treatment technique that coats steel with a protective layer of zinc.
During this process, fabricated steel components are immersed in a molten zinc bath, allowing the formation of a robust zinc-iron alloy coating. This coating acts as a physical barrier against corrosive elements and offers cathodic protection, sacrificing itself to shield the underlying steel from corrosion.
Recent innovations in HDG have focused on alloying the zinc bath with other elements to enhance the coating's adherence and corrosion resistance. For example, incorporating aluminum or magnesium in the zinc bath has shown promising results, improving the coating's durability and performance in harsh environments.
Additionally, integrating duplex coatings, such as silane films, rare-earth conversion films, and self-assembled films, with HDG has significantly improved corrosion resistance and sustainability.
HDG offers advantages such as complete coverage, even in intricate geometries, and excellent abrasion resistance. However, excessively high and low temperatures of the zinc bath can adversely affect the coating properties, requiring careful consideration.3
Plasma Electrolytic Oxidation
Plasma electrolytic oxidation (PEO), or micro-arc oxidation (MAO), is an innovative surface treatment technique that forms ceramic-like oxide layers on steel surfaces.4 During the PEO process, the steel substrate is immersed in an electrolytic bath, and high voltages are applied, inducing micro-discharges that form a dense, hard oxide coating.5
PEO offers precise control over coating properties via electrical parameter adjustments. For example, direct current (DC) mode produces porous, cost-effective coatings. The alternating current (AC) mode prevents electrode polarization and yields thicker coatings with superior corrosion resistance, particularly in bipolar pulse current modes.4
Incorporating nanoparticles or functional materials into the electrolyte also improves corrosion resistance, hardness, and self-lubricating properties.5
While PEO coatings offer excellent corrosion protection, their porous nature may require post-treatment sealing or the application of additional coatings to further enhance their performance in highly corrosive environments.4
Chemical Vapor Deposition
Chemical vapor deposition (CVD) treatment of steel involves vaporizing precursor compounds (halides or organometallic compounds), transporting them to the reactor with an inert carrier gas (such as Argon or Hydrogen), and decomposing them onto the substrate steel to form the desired coating.
Various heating methods, such as inductive, laser beam, or plasma-assisted heating, control the deposition process, while efficient byproduct disposal systems ensure environmental safety and regulatory compliance, enhancing steel component performance and durability.
CVD coatings offer superior protection against oxidation and corrosion in harsh environments with high temperatures and chemical exposure. Their properties can be customized by adjusting precursor materials and deposition parameters to meet specific needs.
For example, SiO2 coatings protect chrome steels in high-pressure CO2 environments. TiB2 and Ti5Si3 CVD coatings extend component lifespan in nuclear power plants, and multi-layer coatings like Al2O3/TiN demonstrate good wear resistance in high-temperature water environments.
CVD also ensures uniform thickness and consistent properties across complex geometries. However, the high process temperatures may limit its application to specific steel grades or necessitate modified techniques like plasma-assisted CVD or metal-organic CVD to reduce substrate temperatures.6
Laser Surface Alloying
Laser surface alloying is a precision surface treatment technique that utilizes high-energy density lasers to melt steel surfaces with corrosion-resistant materials, such as chromium or nickel.
External alloying elements are added to the substrate via a laser-generated melt pool, resulting in a new alloyed layer with an enhanced corrosion resistance of up to 25 %. This method is beneficial when a surface chemical composition and microstructure change are required.7
This technique allows targeted treatment of specific areas, such as high-stress regions, enabling enhanced corrosion resistance without compromising overall structural integrity or performance. However, its high cost and limited treatment area may hinder widespread adoption.8
Future Trends in Steel Surface Treatments
Ongoing research and emerging technologies in steel surface treatments for corrosion resistance are poised to redefine material longevity and environmental standards, offering more sustainable and economical solutions.
One promising area is the development of nanocoatings, which incorporate nanomaterials or nanostructured surfaces. For instance, ZnO nanoparticles enhance steel coating hydrophobicity and maintain corrosion resistance at approximately 1010 Ω·cm2 even after 30 days.9
Nanocontainers encapsulating corrosion inhibitors also offer intelligent coatings for steel protection, releasing inhibitors in response to triggers like pH changes, effectively inhibiting corrosion.10
Another avenue is the exploration of bio-inspired coatings, which mimic nature's ingenious designs to repel water, dirt, and corrosive agents. For example, lignin-based coatings have shown up to three orders of magnitude decrease in corrosion current density, demonstrating significant corrosion reduction in simulated body fluid environments. 9
As advancements in surface treatment technologies continue, their potential to extend the life and utility of steel structures and components across various industries becomes increasingly evident.
Continuous innovation in this field is critical for economic efficiency, safety, and environmental protection, ensuring that steel remains a reliable and durable material for future generations.
More from AZoM: Revolutionizing Medical Devices with Advanced Coating Techniques
References and Further Reading
- Iannuzzi, M., Frankel, GS. (2022). The carbon footprint of steel corrosion. npj Materials Degradation. doi.org/10.1038/s41529-022-00318-1
- Pezzato, L., Brunelli, K., Dolcet, P., Dabalà, M. (2016). Plasma electrolytic oxidation coating produced on 39NiCrMo3 steel. Surface and Coatings Technology. doi.org/10.1016/j.surfcoat.2016.08.057
- Yu, Z., Hu, J., Meng, H. (2020). A review of recent developments in coating systems for hot-dip galvanized steel. Frontiers in Materials. doi.org/10.3389/fmats.2020.00074
- Sikdar, S., Menezes, P. V., Maccione, R., Jacob, T., Menezes, P. L. (2021). Plasma electrolytic oxidation (PEO) process—processing, properties, and applications. Nanomaterials. doi.org/10.3390/nano11061375
- Fernández-López, P., Alves, S. A., San-Jose, J. T., Gutierrez-Berasategui, E., Bayón, R. (2024). Plasma Electrolytic Oxidation (PEO) as a Promising Technology for the Development of High-Performance Coatings on Cast Al-Si Alloys: A Review. Coatings. doi.org/10.3390/coatings14020217
- Sathiyanarayanan, S., Rajagopal, G., Palaniswamy, N., Raghavan, M. (2005). Corrosion protection by chemical vapor deposition: a review. Corrosion Reviews. doi.org/10.1002/chin.200612261
- Rohatgi, A., Bonheyo, G. T. (2022). Laser Surface Processing of Alloys for Corrosion Protection (Final Project Report of Marine Energy Seedling Project). United States. doi.org/10.2172/1878666
- Bonek, M. (2013). Laser Surface Alloying. Encyclopedia of Tribology. doi.org/10.1007/978-0-387-92897-5_687
- Wang, D., Zhao, J., Claesson, P., Zhang, F., Pan, J., Shi, Y. (2024). Green synergy: Eco-friendly, high-performance anti-corrosion and wear-resistant coatings utilizing organosolv lignin and polydimethylsiloxane. Progress in Organic Coatings. doi.org/10.1016/j.porgcoat.2024.108365
- Feng, Y. (2017). Intelligent Nanocoatings for Corrosion Protection of Steels. [Online] University of Calgary. Available at: https://prism.ucalgary.ca/server/api/core/bitstreams/1e6b4071-3269-4645-8066-639bd2594f3e/content
Disclaimer: The views expressed here are those of the author expressed in their private capacity and do not necessarily represent the views of AZoM.com Limited T/A AZoNetwork the owner and operator of this website. This disclaimer forms part of the Terms and conditions of use of this website.