The confocal sputtering technique involves the arrangement of magnetrons inside a vacuum chamber so that it is possible to apply multiple materials onto the substrate without breaking vacuum. This method enables the user to co-sputter, or to form a film from two or more materials at once. It is well recognized for small scale batch productions and for research and development.
Advantages of Confocal Sputtering
Conventional top down sputtering enables sputtering of only one material at a time due to the geometric relation between the magnetron and the substrate. For this type of sputtering, it is necessary to have a target material larger than the substrate to obtain acceptable film uniformity. Moreover, the target material needs be larger than the substrate area.
On the other hand, confocal sputtering involves positioning of the target at an angle with respect to the surface of the substrate. While performing this step, it is necessary to move off the magnetron from the center of the rotational axis and rotate it in the event of deposition to obtain an acceptable uniform film thickness, as demonstrated in Figure 1. This now enables locating multiple magnetrons with different materials at equidistant from the rotation axis of the substrate and each can still deliver a highly uniform film thickness.
.jpg)
Figure 1. Geometric layout of cathode relative to substrate for confocal sputtering.
Cathode Alignment for Optimum Uniformity
Confocal cathode sputtering relies on altering the angle of the cathode target corresponding to the substrate so as to form a highly uniform deposition process. This method needs mounting the cathode at an angle (θ) corresponding to the vertical (y) axis, as depicted in Figure 1.
There is a possibility to receive more material at the inner area of the substrate when compared the outer areas if the substrate is held static. This non-uniformity can be reduced when the substrate is rotated about its own axis with the cathode offset.
The cathode’s tilted orientation helps achieving uniform deposition. The optimization of the tilt angle and the target distance from the substrate can help create highly uniform films. For these reasons, confocal sputtering is capable of often achieving better than 5% non-uniformity in film thickness.
For confocal deposition, the cathode positioning is performed by drawing a line that runs through the cathode center and intersects the y axis. θ is set to 30° to obtain better results, because at this point the only variable left is the distance of the cathode to the substrate (m). In many systems, three or four cathodes can provide the optimum balance over good deposition rates, uniform film thickness, and material flexibility but compromise on the uniformity capabilities of the system owing to the changes in the throw distance.
Sputtering Rate and Target Efficiency
The uniformity distribution of the film thickness pursues a parabolic curve beginning from the substrate center during top down, concentric deposition, as illustrated in Figure 2. The film thickness reduces exponentially from the center during movement towards the substrate’s outside edge. It is possible to move the magnetron farther away from the substrate surface to reduce non-uniformity in film thickness, but results in significant decrease in the deposition rate.
.jpg)
Figure 2. % non-uniformity (y) across the diameter of a substrate (x).
The throw distance to the substrate is capable of dramatically changing the uniformity for a specific area as illustrated in Figure 2. Confocal sputtering enables using a much smaller diameter target material corresponding to the substrate diameter.
The role of rotation in bringing the flat portion of the curve within +/- 5% uniformity is illustrated in Figure 3.
A 4-inch throw distance and a 30° offset for the magnetron are the ideal combination to form the most uniform film and increase the target efficiency with increase in material being used for its intended purpose. This is especially beneficial for precious metals. Moreover, confocal sputtering intrinsically utilizes smaller targets when compared to traditional sputtering.
.jpg)
Figure 3. Graph showing % non-uniformity for a non-rotating substrate in confocal alignment.
The addition of more number of magnetrons to a system must not change the distance from which they are positioned corresponding to the rotation axis of the substrate so as to maintain the complex geometry of the confocal configuration.
Adding the fourth or fifth magnetron will increase the distance in order for all the magnetrons to be at equidistant from the rotation axis. Hence, the use of no more than three to four cathodes is typically preferred for confocal sputtering as the use of more number of cathodes will lead to increased non-uniformity and reduced sputtering rates.
Cathode angle, source-to-substrate distance, and the position where the target’s centerline intersects with the substrate are all significant in creating high quality thin films. One method to ensure adjustability in all of these aspects is to use flex mount cathodes shown in Figure 4, which provide the adjustment required to alter the target angle corresponding to the substrate.
.jpg)
Figure 4. Semicore Flex mounted cathodes in confocal alignment.
Conclusion
From the aforementioned information, it is evident that confocal sputtering offers several benefits to users and extends flexibility to the system. This method improves the yield of the sputtered material and enhances film uniformity. As it can have multiple materials in the vacuum chamber at the same time, it reduces time involved in the formation of complex films, as well as enables co-sputtering to take place. Co-sputtering is greatly recommended for today's sophisticated research and development systems.
About Semicore Equipment
Semicore is a manufacturer and worldwide supplier for the electronics, optical, solar energy, medical, automotive, military and related high technology industries.
Our high-performance production or R&D vacuum sputtering and thin film evaporation systems provide coatings on a variety of materials including plastic films, glass, ceramics, metals and hybrid substrates.
Whether you want to take advantage of our proven industrial solutions for vacuum system automation, process control and supervisory monitoring applications or need to develop some unique new application of your own design you will find Semicore’s staff and facilities to be competent, open-minded and eager to help.
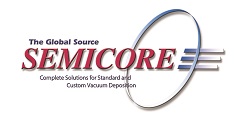
This information has been sourced, reviewed and adapted from materials provided by Semicore Equipment.
For more information on this source, please visit Semicore Equipment.