In a paper recently published in the journal Applied Surface Science, researchers proposed a scalable and environmentally viable method to produce poly(3,4-ethylenedioxythiophene) polystyrene sulfonate (PEDOT:PSS) electrodes on conventional copy paper by implementing modifications on its surface.
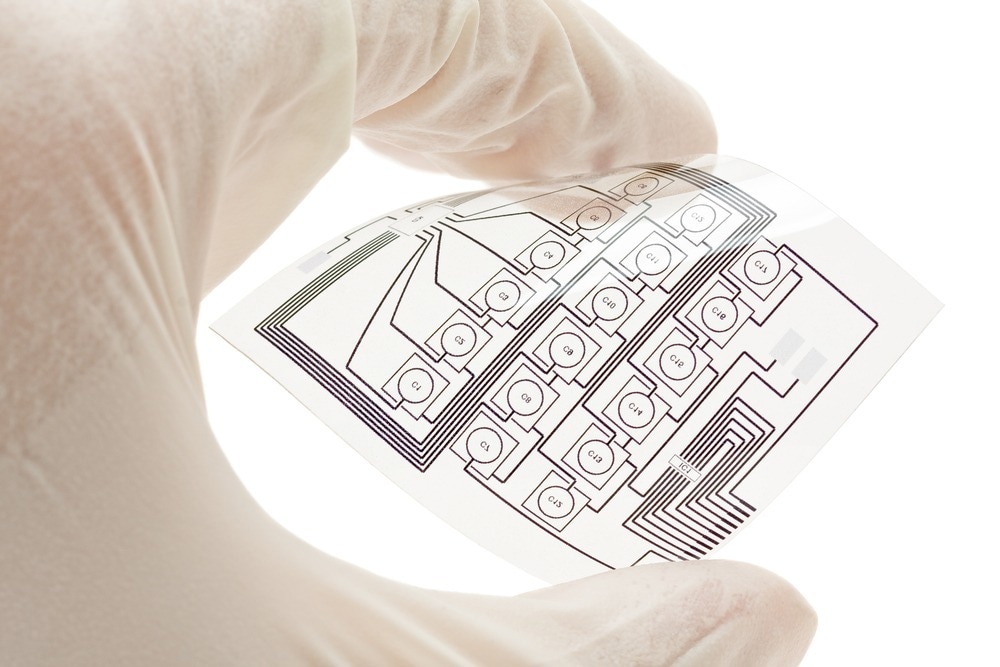
Study: Engineered surface for high performance electrodes on paper. Image Credit: Shawn Hempel/Shutterstock.com
Background
The production of cost-effective electronics has garnered significant attention in the past decades due to the increase in technological applications used in daily life. Presently, many studies are aimed at discovering novel pathways to synthesize smaller, lighter, high-performance devices. Therefore, the utilization of flexible, thin substrates facilitates large-scale device manufacture with relatively low-cost processes like printing.
Biopolymers, such as cellulose, lignin, and keratin, are some of the materials that fulfill the requirements of natural, sustainable, and recyclable materials contributing to minimal electronic waste. In various applications such as solar cells, batteries, and sensors, cellulose processed in a paper sheet form, has been successful as a substrate. An ideal electrode coating process must be inexpensive, contain minimum production steps, and minimize waste by using environmentally feasible materials while also ensuring product recyclability.
About the Study
In the present study, the team used two cellulose derivatives, hydroxyethylcellulose (HEC) with a 2.5 molar substitution (MS) of hydroxyethyl groups and hydroxypropyl cellulose (HPC). The copy paper used was acid-free, consisting of an alkaline reserve. HEC and HPC solutions were synthesized at three concentrations, respectively 4%w, 3%w, and 2%w for HEC and 5%w, 4%w, and 3%w for HPC. A PEDOT:PSS solution was prepared for electrode realization through dilution of PEDOT:PSS in 2-propanol in the ratio of 1:5 while adding 5% dimethyl sulfoxide.
A rheometer was used for the rheological characterization while the planarization solution was deposited using an automated blade/slot die coater. The cup test and the Cobb180 test were utilized for the water vapor barrier and water uptake measurements. Subsequently, the PEDOT:PSS electrodes were fabricated on two substrates, one uncoated copy paper and the other coated with 20%w of HPC (HPCLMW20%w). Furthermore, a four-probe system measured the resistivity of the PEDOT:PSS electrodes. A custom apparatus was used to perform the cycle bending tests, while a field emission scanning electron microscope (FE-SEM) was used for the morphological characterization of the samples.
Observations
At greater polymer concentrations, a higher zero-rate viscosity was seen. Moreover, it was observed that the polymeric solutions remained stable at 100 s-1. Additionally, the morphological assessment determined that the HEC 4%w solution was the least effective, as it was both, energy-consuming and troublesome to prepare.
Moreover, at equal concentrations, HPC was anticipated to be more efficient in wetting the surface of the paper than HEC. Using the HPC was favored since it also had a more suitable surface tension for its application on paper compared to HEC. Furthermore, the Cobb180 tests determined that the paper displayed superior characteristics when treated with HPCLMW20%w. The water vapor transmission rate (WVTR) values exhibited a similar qualitative trend as seen in the Cobb180 test, with the HPCLMW20%w coating providing the most substantial enhancement in barrier properties.
Therefore, considering these results, HPCLMW20%w was selected as the choice of paper coating for printing PEDOT:PSS electrodes with large areas. Moreover, the FE-SEM images of the PEDOT:PSS electrodes showed that one HPCLMW20%w layer was adequate to warrant a homogeneous polymer deposition. The thick composite interlayer consisting of HPCLMW20%w and the paper cellulose matrix appeared to be a significant requirement for depositing a denser and packed PEDOT:PSS film.
Additionally, improved conductivity was exhibited by the coated samples in comparison to the uncoated ones, and the electrodes were confirmed to be stable in different environmental conditions. At lower strains, the electrode on uncoated paper attained the breaking point against that on the coated one. Furthermore, a linear increase in the resistance was observed with elongation until the breaking point was reached. Neither the non-coated nor the coated electrode attained the rupture point, implying favorable mechanical operation under external strain.
Conclusions
To summarize, the researchers obtained a suitable surface to effectively deposit the conductive polymer with the use of a cellulose derivative-based polymer in coating the paper substrate using the blade-coating method. HPCLMW20%w, was determined as the optimum coating solution since it resulted in the perfect coating of the fibrous structure of the paper, thereby enhancing its moisture barrier characteristics.
The electrodes synthesized on coated paper further exhibited a reproducible and stable electrical response to those on uncoated paper. According to the authors, the improved electromechanical features of the electrode could be a substantial advantage in its usage in wearable devices. Furthermore, its durable and reproducible performance could support effective integration in the energy storage or sensor systems, resulting in stable signals as well as reliable responses.
More from AZoM: Strong and Heat-Resistant Synthetic Fiber Kevlar and its Composites
Disclaimer: The views expressed here are those of the author expressed in their private capacity and do not necessarily represent the views of AZoM.com Limited T/A AZoNetwork the owner and operator of this website. This disclaimer forms part of the Terms and conditions of use of this website.
Source:
E. Palmieri, et al., Engineered surface for high performance electrodes on paper, Applied Surface Science (2022), DOI: https://www.sciencedirect.com/science/article/pii/S0169433222026459?via%3Dihub